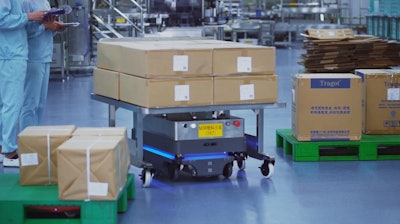
Reducing reliance on human labor for dull, though complex and potentially dangerous material handling tasks is one way to keep production high and costs low — requirements to compete in today’s market. For example, when Chinese herbal supplement manufacturer Infinitus overhauled its Jiangmen facility in Guangdong in 2017, it realized that automating its intralogistics processes could eliminate production bottlenecks and wasted manpower. Relying on manual processes was limiting productivity and keeping costs high since they were paying human workers to move materials around the plant. Infinitus initially looked into automated guided vehicles (AGVs) but it realized that installing guided tracks into the factory floor would prove too disruptive, time consuming and costly.
AMRs Over AGVs for FMCG Companies
After encountering autonomous mobile robots (AMRs) at a packaging tradeshow in 2018, the company decided they were more in line with the company’s requirements for flexibility and efficiency. In March 2019, Infinitus purchased three AMRs, which employ a sophisticated mix of sensors, cameras, data and on-board computers to autonomously determine the most efficient route in a constantly changing environment and to move out of the way of any obstacles. No infrastructure changes are required, meaning they could be quickly and easily deployed. The AMRs — each with a 200kg payload and various top modules enabling multiple material handling applications — were deployed in the packaging production line, where there were more than 10 types of material involved in the packaging process for its oral liquid.
As Infinitus realized, the main benefits of the AMRs for FMCG companies include:
Adaptability/Flexibility: In today’s environment, with consumer and market demands fluctuating, adaptability is no longer an advantage but a requirement for survival. By implementing the latest automation technology, like AMRs, manufacturers can reduce costly and time-consuming manual transportation, supporting a lean approach and increasing adaptability. Even better, the AMRs can be redeployed for different tasks with customized top modules such as pallet stackers and hooks, making each one flexible and able to adapt to changing processes, as needed.
Safety and productivity: The built-in sensors, cameras, and advanced control frameworks of the AMRs enable them to analyze their surroundings, safely avoid obstacles, and calculate an optimal route to a given destination. This advanced technology is simple to harness through a user-friendly interface that facilitates a high degree of collaboration between the human workers and the robot. Advanced features ensure that the robots can independently and logically perform tasks safely and efficiently. Easy-to-program fleet management software holds the three AMRs together with centralized control. At Infinitus, the software coordinates the three AMRs according to the production needs of the workshop, managing task priority and designating the most suitable robot for any given task. Because the plant is a dynamic hive of activity, obstacles such as personnel, equipment, and pallets often appear in the robots’ path and may even cause congestion. The software can direct the robots to safely navigate multiple paths and intersections.
Cost optimization: The pressure to keep costs low but quality high is here to stay. Couple this with foreign competition, tariff uncertainty and labor skill gaps, and the FMCG industry finds itself in an uncomfortable position. However, AMRs can help by replacing inefficient manual processes with efficient, autonomous production process. Not only does this reduce production bottlenecks and delays caused by human error, it also helps manufactures combat worker shortages by allowing skilled workers to complete value adding, complex tasks instead of manual transportation. Creating a safer environment with the AMRs means that costs can also be saved by reducing lost workdays and fines due to workplace injuries.
Increased uptime: As discussed previously, the onboard sensors and cameras used to operate means no wires or tracks are required, which limits the downtime that can occur when implementing other technology. AMRs also have an intuitive interface, making the robots easy and quick to set up and deploy. They can also work around the clock, ensuring a steady material flow. Rather than stopping when approaching an obstacle, they can calculate alternative routes without disrupting the workflow. In addition, AMRs can be switched to perform new tasks with relative ease, increasing uptime.
Since installation in March 2019, the AMRs have significantly improved both intralogistics and production levels for Infinitus. They have significantly reduced the need for manual labor, freeing up personnel for more advanced technical work like material inspection. This allowed Infinitus to utilize talent more effectively and empowered its personnel to engage in work that creates more value. Also, according to Zhou Chaowei, senior director of the Infinitus Xinhui Production Center, current production levels are 3.5 times higher than before AMR deployment.
The opportunities Infinitus realized with AMRs are widely shared across other FMCG companies that have embarked on digital transformations where robotics play a key role. What visionary companies have seen is that AMRs can help automate areas and tasks never thought possible before. Being nimble and agile, AMRs can go into the heart of production and packing areas to bring forward and back both high and low volume consumables to keep production running. These companies envisioned a fleet of AMRs simultaneously moving components to multiple production lines to speed a change-over cycle and boost capacity utilization. This is only one area AMR can help automate, however.
Flexible AMRs facilitate myriad FMCG applications
FMCG companies like Infinitus can customize the flexible and open platform AMRs with top modules to create application specific to their production facilities, such as:
- Conducting quality sample picking and delivery to storage
- Pallet transfer from end of line Palletizer to the Warehouse
- Moving carts with obsolete packaging and used pallets to the storage areas
Enabling more efficient order picking in finished goods area or distribution centerVolodymyr Vovk
- Delivering finished goods to the staging area for container or truck loading
As a result, AMRs will continue to bring the decreased complexity, lower costs and higher productivity FCMG companies need to compete in the increasingly complex and competitive global business environment.
Volodymyr Vovk is global account director for FMCG at Mobile Industrial Robots