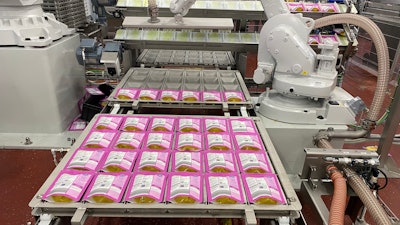
For any production company, constructing a greenfield plant creates the opportunity for it to be ‘born digital’ and immediately benefit from the implementation of advanced automation software and technologies. Whereas historically, automation was focused on ensuring production meets required specifications and safety parameters, now manufacturers are finding that implementing a broad range of digital technologies can support long-term operational excellence. There are some obvious drivers for this change. Global competition has placed greater emphasis on plant efficiency, availability and throughput, which in a crowded marketplace, can mean a difference in profitability and time-to-market. There are also new societal drivers, such as rising energy costs and the need to increase sustainability.
To help meet these challenges, plant operators are now increasingly looking to specify advanced digital technologies during the plant design phase. This includes the implementation of modern supervisory control and data acquisition (SCADA) solutions that can integrate all parts of production, equipment and systems, as well as collect and analyze key performance data, and then present this to operators and management to identify issues, support improved decision-making, and drive increases in availability, throughput and overall equipment effectiveness (OEE). A great example of this can be found at FEI Foods, which has implemented a new generation of SCADA/HMI solutions for plant monitoring and control to support desired increases in throughput and efficiency at its new processing and packaging facility.
Based in South Wales, UK, FEI Foods is Europe’s largest producer of ready-to-eat rice and grain pouches. The company developed a unique process for producing light, fluffy rice that doesn’t stick together in microwavable pouches and was the first to market with a recyclable ready-to-heat pouch. Due to the popularity of its products and increasing demand, the company’s existing production facilities had been operating at near capacity for several years. This prompted the decision to design and build a new 250,000 sq ft state-of-the-art factory in Llantrisant, Wales.
A completely new plant provided FEI Foods with the perfect opportunity to digitally transform its existing operational technology and practices with the implementation of advanced automation software to help maximize plant efficiency and productivity. A key focus was improving access to data and transfer of data to support inventory management and for packaging production and printing. At the existing FEI Foods production facilities, all inventory control declarations and the sending of production information to printers for packaging and labelling was performed manually. FEI Foods executives wanted to fully automate this process to increase efficiency and remove the potential for human error. Another key requirement was the need to provide both operators and executives with full visibility of the production process and OEE, as well as access to key operational data on which continuous improvement decisions could be based.
To provide the necessary information for operations and engineering teams, an integrated SCADA solution was needed that could interconnect all the new automation equipment over the factory data communication network. In addition, the new solution needed to interface with the FEI Foods enterprise resource planning (ERP) and inventory control systems, as well as printing, labelling and applicators. This would enable automatic production declarations to be performed at the end of every batch.
PLATCON, an automation and electrical design company, was chosen as the system integrator for the project, and selected the Movicon.NExT™ SCADA platform to meet the stringent requirements of the new factory. The SCADA software connects to programmable logic controllers (PLCs) that control the different production processes, collects process information from the automation equipment and then stores it in SQL and ORACLE databases. It also communicates with the inkjet and labelling equipment to provide updated information dynamically during production.
To eliminate the inefficiency and inconvenience of a manual inventory system, Emerson worked with PLATCON to develop a webservices interface to allow the Movicon.NExT platform to communicate with the inventory control system. This enabled operator intervention steps and potential errors to be eliminated by automating production declarations to the ERP system at the end of every batch. The new system also enabled the automatic transfer of production information to inkjet printers, case and pallet labellers and barcode scanners. Previously this data, needed for batch numbers and best-before dates, was modified at the end of every batch manually by operators.
The SCADA solution is connected to the factory data network, and six monitors in the control room give the operations team full process visibility. Moreover, 10 web clients have been installed that provide secure remote access, enabling accredited operators to view and interrogate the process. With the Movicon.NExT platform, all the stand-alone automation systems have been integrated, allowing communication with each other via Ethernet and providing complete visibility of the process and product data tracking. To understand the OEE and performance of the facility, the Movicon Pro.Lean™ module connects to 20 pieces of equipment. Key performance data is collected and analyzed to calculate the OEE and measure downtimes. This provides FEI Foods with process improvement insights, and helps the company reduce equipment failures and improve OEE.
“When we invested in a fully automated production process, we aimed to create the most efficient and flexible manufacturing facility possible to enable us to meet market demands,” said Dean Miles, Engineering Project Manager, FEI Foods. “The SCADA system from Emerson enabled us to eliminate manual processes and increase our speed of response and decision-making, while complete visibility into equipment downtime and machine health has allowed enhanced productivity through timely intervention. Also, the Movicon Pro.Lean software module helps us to identify areas where we can further increase OEE.”
In addition to providing the functionality to meet the requirements of FEI Foods, the Movicon.NExT platform proved to be easy to use and a powerful development tool for system integrator PLATCON. The software offered a very intuitive configuration environment, helping PLATCON design engineers to complete the project faster and more easily.
“The power and flexibility of Movicon.NExT has allowed complex process-oriented operations to be reliably executed on demand. This gives the Movicon.NExT project additional functionality over and above what we would class as a standard SCADA application project,” explained Stephen Vincent, technical director at PLATCON.
For FEI Foods, implementing modern SCADA technologies enabled the company to respond to growing global demand as well as competition, with increased efficiency, availability and productivity, while also meeting sustainability goals.
Ajay Rana is the Global Industry Marketing Manager, Food & Beverage, CPG, and Life Sciences at Emerson.