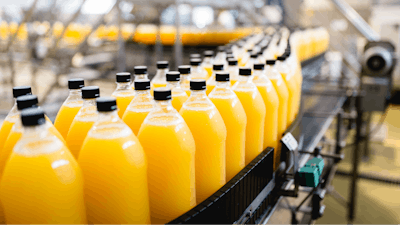
In a fast-paced consumer market rife with global issues, the food and beverage industry faces a multitude of challenges in upholding food safety and compliance, while driving operational efficiency.
According to a 2022 State of Food Manufacturing Report by Clear Seas Research, 78% of respondents were interested in improving supply chain management. Further, 61% of respondents stated a need to increase flexibility on existing production lines.
For food and beverage producers, relying on outdated supply chain technology and manufacturing processes present severe repercussions, such as: food spoilage and write offs, regulatory and compliance violations, and compromised consumer trust. Given the risks associated with obsolete technology and burdensome manufacturing processes, investing in advanced supply chain systems has become an imperative for the sector.
In the realm of supply chain technology, implementing a multi-enterprise platform is something that may not immediately come to mind for food manufacturers. With heavy emphasis on upgrading dated ERPs or complex APS systems, many don’t realize that purpose built operations tools, or robust, real-time collaboration can unlock even more value from their investments to drive sustainability and efficiency across their supply ecosystem to:
- Improve the shop floor performance and operational efficiency of its outsourced manufacturing and packaging partners; and
- Drive easy, scalable integration with trading partners to support real-time, high fidelity and dynamic collaboration and synchronization
First, let’s look at three ways that a multi-enterprise platform can optimize the shop floor performance of manufacturing partners, such as contract packagers and external manufacturers.
How a Multi-Enterprise Platform Can Improve Food Manufacturing Performance
1. Maintain Safety and Quality: Many third-party partners, such as co-packers and contract manufacturers (aka external manufacturers), lack a modern and robust digital solution to manage their production operations. Outdated, obsolete manual workflows can lead to inventory expiry, food spoilage and an overall lack of quality control. Similarly, systems not designed for food and beverage manufacturing and packaging struggle to offer data visibility into the movement and tracking of these goods throughout the production process. This provenance often falls to spreadsheets and paper-based processes, which can add costly delays and increase room for human error.
A multi-enterprise platform offers a purpose-built solution for food and beverage manufacturing and packaging service providers that empowers them to track the entire production workflow, enforcing quality compliance processes and maintaining safety protocols. These solutions ensure that production lines can focus on being efficient and accurate, without being burdened by manual checks related to quality control.
By investing in best-of-breed supply chain technology, manufacturing partners establish robust quality control mechanisms, mitigate risks, and ensure the delivery of safe, high-quality products to consumers.
2. Ensure Compliance: With ever-evolving food safety regulations, outdated technology hinders compliance efforts by impeding traceability, accurate record-keeping, and efficient recall management. Non-compliance not only jeopardizes public health but also exposes companies to legal liabilities, reputational damage, and potential financial penalties.
Stringent regulations governing food safety and traceability, such as FDA regulation and GMP certification, necessitate the adoption of technologies that can adequately support and enforce these processes.
Purpose-built solutions for manufacturers and packagers are able to support a myriad of production-related quality functions, such as track and trace, release controls, and validation support. Systems such as these play a vital role in helping manufacturers and packagers meet regulatory requirements, streamline compliance processes, reduce administrative burdens, and proactively address potential issues.
3. Increase Efficiency: Unwittingly inefficient production operations often rely on manual processes to track production status and inventory movement, leading to limited automation and restricted data visibility, which in turn impedes businesses from achieving their full potential for efficiency and growth. They are forced to cope with daily issues of production delays, increased labor costs, and reduced OTIF. Optimizing operations through real-time production inventory tracking and automated data flow can minimize downtime and reduce costs.
How Your Bottom Line Benefits From Multi-Enterprise Collaboration
By enabling data visibility for all the manufacturing and packaging partners in a supply ecosystem, a multi-enterprise collaboration platform acts as a single source of data truth for all parties. Using the real-time data transparency enabled across the entire network, food and beverage manufacturers can plan and execute orders with greater confidence, accuracy, and agility,, while optimizing the capacity of their outsourced partners.
The level of data visibility offered by a multi-enterprise platform can yield substantial cost savings and operational efficiencies all throughout the ecosystem. According to research by PwC, investments in supply chain visibility generate 8% additional revenue and reduce costs by 7%.
In addition to these financial gains, food and beverage manufacturers can preserve brand reputation, ensure inventory longevity, and maintain food sustainability.
How Technology Can Preserve Food Safety and Sustainability
A report by the Natural Resources Defense Council revealed that America wastes approximately 40% of its food. Not only is this a poor reflection of our ability to manage the use of the planet’s limited resources, the amount of wasted food also contributes to significant financial losses for manufacturers, distributors, and retailers.
Manufacturers and suppliers who embrace multi-enterprise collaboration and technology have the unique opportunity to enhance food safety and compliance, as well as drive operational efficiency and cost savings for itself and its trading partners. Automation of manual processes, real-time data visibility, and predictive analytics enable companies to optimize inventory management, minimize waste, and improve forecasting accuracy. Consequently, labor costs are reduced, productivity is increased, and overall operational efficiency is enhanced.
For those managing food and beverage manufacturing supply ecosystems, investment in modern supply chain technology, especially in the realm of multi-enterprise collaboration, is no longer optional but necessary. Outdated technology poses significant risks to food safety, compliance, and operational efficiency. By embracing technology solutions, companies can mitigate these risks and ensure the highest standards of excellence. Real-time monitoring, end-to-end traceability, and automated compliance management safeguard both consumers and businesses, ensuring delivery of safe, high-quality products while driving competitive advantage.
Christine Barnhart is vice president of product marketing at Nulogy.