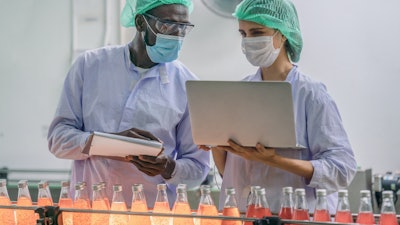
Modern-day businesses are customer-centric in approach. If the customer is not satisfied with the quality standards of a product, a brand cannot make an impact on the consumer. Quality issues can arise at any point in the supply chain, and it is critical to identify them as early as possible to prevent excess time and costs, mitigate risks to reputation, compliance, and ultimately, food safety.
Today’s consumers and businesses demand an unprecedented abundance of products, whenever and wherever they need them. Add to this, the complex and long-tail nature of modern supply chains, continued pandemic disruption, regulatory and operating differences within specific regions or countries, and you can see how it is difficult to maintain and enforce a consistent level of quality for your product.
What are the benefits of quality management?
Quality management is one of the most important factors for businesses to ensure, from grower to consumer. Implementing improved quality management not only minimizes the number of quality issues but ensures that manufacturers and suppliers all understand what is expected of them, so you can maintain a consistent standard of quality at every stage. Improving operational performance and mitigating regulatory, legal, and food safety risks.
How to manage product quality?
The effectiveness of quality management in your supply chain will depend on the systems you have in place. Manual processes and protocols can cause errors, waste time, and consume resources. Modern technologies and strategies will help to transform your supply chain and maximize performance.
1. Time
Manual processes are inefficient and time-consuming. By automating your quality management, you eliminate the need for manual data collection and time-consuming emails or calls. Streamlining your processes will allow your team to focus on more valuable tasks. 83% of supply chain leaders expect that digital will be the predominant supply chain model in the next 5 years (MHI Industry report 2021)
2. Supplier performance
Product quality is a collaborative endeavor. Your suppliers need to understand your requirements if product quality is to be achieved. Regular audits and assessments of supplier performance will help to identify problematic trends, allowing you to put in place a corrective action plan when issues arise. Supplier quality agreements will define what good and bad looks like, and how suppliers will be held accountable for their commitments.
3. Legal requirements
A supply chain can present significant legal and compliance risks. From a quality perspective, food fraud and food safety are a big risk to businesses. It was already a serious issue before the pandemic, but the rise in global food fraud has increased substantially since COVID-19 struck in 2020.
Legal frameworks can, and often do, place the primary responsibility to prevent fraud on food business operators, through traceability requirements and requirements to adhere to good quality management practices, which include the adoption of Hazard Analysis Critical Control Point (HACCP) principles.
4. Visibility of data
Having complete visibility and capturing food quality issues in a centralized format can have a massive impact on improving quality across your supply chain. Powerful and user-friendly analytical tools make it possible to compile large sets of unstructured data and extract useful insights to support your decision-making.
Example of custom insight checks using Greenlight Quality Management
5. Checks
Food quality isn’t just about safety. It’s offering the highest quality possible to your customers and ensuring everyone is on the same page when it comes to quality checks. A quality management solution can capture quality issues, anywhere in your supply chain, fully documenting these issues including uploading pictures for detailed information.
Example of in-app quality checks using Greenlight Quality Management
The Final Word
Quality management is a journey that everyone is on together, all stakeholders need to understand what is expected of them to uphold the highest quality standards. As the complexities of the supply chain continue to grow along with consumer expectations, implementing a solution that can tackle the key areas we have mentioned is crucial not only to minimize the number of quality issues, but also to save time, mitigate risk and ensure visibility of anything that’s out of specification.
This blog was written by Muddy Boots by TELUS Agriculture. Muddy Boots helps customers produce safer, more sustainable food through supply chain and farm management software that delivers insights, drives better decisions and enables collaboration across global supply chains.