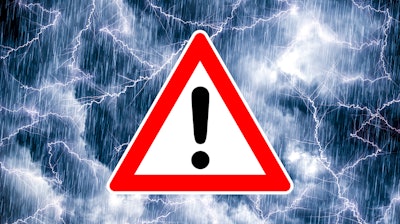
In a globalized world, the food manufacturing industry plays a vital role in ensuring food availability and safety. When weather threatens food production and distribution, manufacturers must take action to mitigate any risk. Within the United States, many manufacturing facilities that are regularly affected by hurricanes and tropical storms rely on professional weather services for 24/7 decision support and hourly weather updates. We often hear from multinational consumer foods manufacturers that they are looking for ways to improve their operational workflow in the event of a critical weather emergency. Here are some best practices for managing operations, no matter the weather.
1. Global Coverage Counts
While the headquarters of a business may be in one country, production and supply chains can be rooted globally. Three significant weather events in 2020 threatened operations in East India and South Korea for many of our manufacturing clients. These were Super Cyclone Amphan, and Typhoons Bavi and Maysak.
The need for worldwide coverage is paramount if you have international facilities. All of your facilities deserve the same level of operational support. That can be a challenge as the quality of the alerts and forecasts is often limited to what the official agency in each country delivers, which means inconsistency with forecasts, language and time zones.
Access to consistent, accurate data across all tropical basins ensures every facility is treated with equal consideration and international business can progress.
2. Safety First
Weather can seem unpredictable. Not being able to anticipate threatening events is every company’s nightmare, but until you experience something first-hand, or conduct a vulnerability assessment, it is hard to know what plans should be developed. With a variety of weather events posing threats to facilities — hurricanes along the Gulf coast and Atlantic seaboard, typhoons in India and Asia, wildfires in the western U.S., to name a few — safety of personnel is a top priority.
Protecting your staff before and during an emergency relies on accurate forecasting. A good example of this is the use of risk alerts via SMS. This is a quick and easy way to provide information to all staff and can quickly become a critical tool for managing the workflows of nearly every department within an affected facility.
Outside of facilities, manufacturers can also use these alerts when their product is in transit. Having information on travel routes not only protects the product, but more importantly the transport teams. Alerts not only improve the manager’s efficiency, but everybody else’s efficiency as they can receive alerts right away.
3. Don’t Expect This Year to Be Like the Last
While we can learn from history and make better predictions, it’s important to stay prepared no matter what previous years looked like. 2020 was a challenging year — from a record thirty named tropical systems with twelve making landfall over the U.S. — the hyperactive Atlantic tropical season kept everyone busy. To cope with the increased number of threats, it is a best practice to schedule conference calls with a professional weather partner during weather events to discuss the probabilities of how the weather conditions would affect their facilities or assets with managers from key operational departments: supply chain, operations, facilities, emergency management
This allows managers to ask questions that specifically affect their side of operations, and to receive answers from a meteorologist that knows the critical aspects of your operation and facilities.
The right information is crucial for planning, and making hard decisions, such as whether to evacuate or continue operations. These ‘go or no-go’ decisions can make a difference of millions of dollars at the end of the year.
4. Reacting to a Changing Climate
Mirroring the record-breaking tropical storm season, 2020 saw a similar increase in wildfires across the U.S. While our thoughts first go to flames as the immediate risk, it’s important to remember the detrimental effects smoke can have on air quality. The effects of smoke are often felt well beyond the immediate perimeter of the fire. StormGeo provided alerts for projected smoke spread and air for a manufacturing facility in the Midwest, which was affected by smoke coming from coastal fires. Air quality can have detrimental impacts on staff working outside. Monitoring air quality, even in areas that might not typically be considered at risk for fire damage, enables the protection of workers’ health above all else. For facilities closer to the actual fires, forecasts for wind and atmospheric conditions are recommended to stay on top of the proximity and spread of the blazes.
Every year, manufacturers face new challenges, but at the same time, their experience grows and enables them to face down those challenges. These companies Ian Nicolson
A native of Scotland, Ian Nicolson is a Senior Industry Manager at StormGeo, a 24/7 provider of weather intelligence. He has a long-standing track record providing solutions to manufacturing companies, helping them solve their greatest challenges while offering new and innovative strategies to streamline operations and grow business.