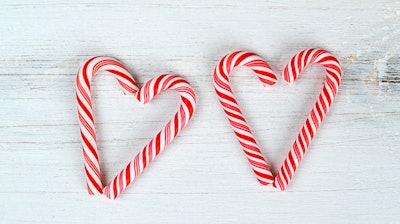
As we head into Q4 and approach the holiday season, it seems like the only certainty is prolonged uncertainty, which makes year-end business planning and forecasting particularly difficult. For many food manufacturers, the winter holiday months may be the busiest time of year, given supermarkets’ and restaurants’ push to meet consumer demand for lavish, decadent food—and lots of it. We also have to grapple with inflation, which has driven up prices of raw ingredients, packaging materials, and manufacturing equipment. Of course, many food manufacturers are struggling to find new machinery or maintain the machinery they already have, given the persistent supply chain disruptions and shortages. To top it all off, a potential railroad workers’ strike in the United States threatens to derail 30 percent of America’s freight transport. All in all, this holiday season is poised to be a challenging one for food manufacturers.
Let’s take a clear look at the supply chain challenges facing food manufacturers and outline some actionable strategies to mitigate these challenges in the short-and long-term.
State of the Supply Chain
While some supply chain disruptions appear to have abated since their peak earlier this summer, there are still plenty of economic indicators that are giving economists and food manufacturers pause. For some of the most popular commodities, supply is low, and prices are high—like wheat, whose price reached a three-month high in early October. This volatility comes against the backdrop of the war in Ukraine: a country that usually produces an estimated 40 percent of the world’s wheat supply. If this high-cost, low-availability trend continues, it could spell trouble for the holidays, as many popular food items like stuffing, bread pudding, and dessert items typically require wheat-based ingredients.
Even if food manufacturers can identify and engage with commodity suppliers, it doesn’t mean they’ll be able to pay for the raw ingredients they need to continue operating. Many economists believe inflation is on the verge of spiraling out of control. As of October 13, the United States’ year-to-date inflation rate through September was a whopping 8.3 percent, dramatically higher than the Federal Reserve’s typical goal rate of 2 percent annually. For the food industry in particular, the trend is much the same—within the month of September, the price of fruits and vegetables soared by 1.6 percent. These figures might not seem like a lot at face value, but taken at scale, they have the potential to do real damage to food manufacturers and their businesses. While no economist has the ability to predict the future, the broad economic trends we’re seeing aren’t painting a very optimistic picture for the rest of the year.
Another factor shaping the ongoing supply chain disruptions is the heightened costs associated with shipping and freight. While gasoline and diesel prices may have dipped below the peaks we saw in the spring, they’re still high enough to make freight and shipping more challenging than usual for food manufacturers. According to the U.S. Energy Information Administration, the prices of diesel and gasoline are up 1.6 percent and 0.6 percent, respectively, as of mid-October. We haven’t seen the last of shipping challenges, either—the Organization of Petroleum Exporting Countries (OPEC) announced in early October that it was significantly curtailing oil production, which could cause fuel prices to skyrocket again. Ultimately, the volatility in fuel prices creates a whirlwind of challenges for food manufacturers as it becomes much more difficult to plan and budget for freight and shipping.
Between scarce commodities, inflation, and fuel prices, it’s a challenging time for food manufacturers—especially within the broader context of the looming holiday season, when many Americans go all-out for special occasion meals like Thanksgiving and Christmas.
How Food Manufacturers Can Move Forward
Now that we’ve set the table with today’s challenging landscape of food manufacturing, let’s dive into some mitigating strategies manufacturers can employ to help stay afloat and future-proof their organizations. These strategies aren’t quick fixes and can’t be accomplished overnight—if you know of any such strategies, do let me know—but they are certainly a step in the right direction towards establishing a more efficient, adaptable organization that can better withstand economic challenges like the ones we’re seeing today.
First, food manufacturers should consider implementing automation wherever possible. Not only will automation deliver high-quality, consistent results, but it can allow manufacturers to do more with less by streamlining processes or tasks that were previously done manually. In an industry where every margin matters, ensuring standardized and optimized batches and efficient, productive processes are paramount. For food manufacturing in particular, automation can bring the benefits of enhanced traceability, optimized quality control, better workplace safety, and improved sanitation. Leveraging automation is a good step in the right direction towards enabling a more efficient, flexible manufacturing operation that can respond nimbly to economic shifts.
Another strategy to consider involves the diversification of ingredients and vendors. There’s no denying the convenience and consistency of relying on the same partners and producers month after month, but in doing so, food manufacturers could be inadvertently signing up for more risk and cost than they can stomach. Vendor lock-in should be avoided wherever possible, and at the very least, manufacturers should consider having secondary or tertiary options for the ingredients and products they need the most. Having pre-vetted alternates could make all the difference when the next wave of destabilization hits the industry.
This next future-proofing strategy is one that many food manufacturers are likely already doing, but it bears reiterating: try to reduce waste where possible. Beyond being a good business practice, reducing waste means making the most of your inventory and not letting your expenditures go out the door in a trash bag. For food manufacturers, one effective way to mitigate economic challenges or uncertainty is by ensuring their plants are running as efficiently as possible and maximizing the mileage from their ingredients and materials.
Finally, a potential future-proofing strategy food manufacturers should consider is the practice of over-communicating with employees, partners, vendors, and customers. As we’ve seen, there are numerous factors outside manufacturers’ control—the one thing they can control is how they communicate. Be upfront if you’re going to miss a deadline or fall short of a quota. Give teams as much notice as possible when they will be needed to work overtime. Even when you’re delivering bad news, your partners, employees, and customers will appreciate your candor and transparency. Upfront communication is a must-have when it comes to developing mutual trust—and trust (in your word as a leader, in the value proposition of your business, in your products) can make all the difference when times are tough.
Final Thoughts
Nobody knows how this (or next, or any) year will pan out, and there are certainly economic indicators that have given experts cause for concern for the rest of 2022. By working with advanced technology, diversifying where possible, operating more efficiently, and over-communicating, food manufacturers can set themselves up to weather the storm as best as possible—and prepare for the next one.
---
Nic Azad is TrakSYS Communications lead at Parsec Automation.