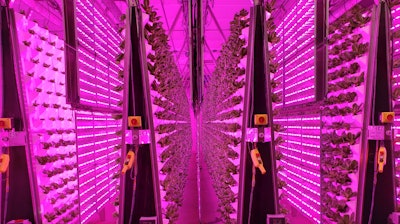
A 2017 report from the World Health Organization found 11 percent of the global population, an estimated 815 million people, faced issues with hunger. The same report said malnutrition threatened the health of millions of people, and cited climate change and violent conflicts as reasons behind the disturbing trends.
Things might be even worse for the next generation. The world population is expected to increase by another 2 billion people by 2050, and the demand for food will rise along with it. “Given population growth and rising incomes, it is estimated that demand for food will rise by 70 to 100 percent by 2050,’’ the U.S. Department of Agriculture said. “To meet this need, the United Nations estimates that production in developing countries will need to double.”
One part of the solution to meet the current and impending food demand can be found in the fast-growing vertical farming industry. Urban farms can be found in many U.S. cities, including Chicago, New York, and Cleveland. Other nations have also seen vertical farming businesses sprout. Singapore, which has the world’s third-highest population density, has more than 30 vertical farms. Japan has more than 200 lettuce factories, with that number expected to double by 2025.
Business Wire reported vertical farming values in the United States are expected to reach $3 billion by 2024, growing at an annual growth rate of 24 percent through 2024. The global market is expected to reach $12.77 billion by 2026, according to Allied Market Research.
Living Greens Farm, based in Faribault, Minnesota, is showing how its done. In a 7,000 square foot building, the company is showing the world what the future of farming looks like. Combining aspects of science, agriculture and technology, the company uses an aeroponic system to produce fresh salads, microgreens, and herbs.
By growing vertically, Living Greens Farm uses 98 percent less land, 95 percent less water and 60 percent less labor than conventional farming methods. The company sits squarely at the intersection of demand, technology, and innovation, with a proven system that will help provide a solution to a global challenge.
“We whole-heartedly believe indoor/vertical farming is the path forward for agriculture,” said Nate Klingler, Vice President of Business Development for Living Greens Farm. “Demand for food is growing, and demand for safe, delicious, and healthy food is growing at an even faster rate.”
The “Air Grown” vertical system at Living Greens Farm reduces the need for land, energy, water, and space. The company grows leafy greens such as Romaine, Butter Lettuce, mixed greens, and basil.Photo courtesy of Living Greens Farm
All Grown Up
Living Greens Farm uses an aeroponics system in which plant roots remain in the air 99.9 percent of the time. The plants thrive under the perfect balance of light, air, humidity, and nutrition.
Dana Anderson, who founded the business, worked on farms as child in Minnesota and was inspired by a NASA study that sought methods for growing plants in space. He started developing the technology in the garage of his Minnesota home before it officially launched in the 2012.
“We didn’t invent aeroponics,’’ Anderson said. “But we invented how to commercialize it. We feel aeroponics is the fastest and most disease-resistant way to grow.”
According to the Allied Market Research report, aeroponics is projected to have a compound annual growth rate of 26 percent through 2026. The report said aeroponics is expected to have stronger growth than other forms of soil-less gardening, hydroponics, and aquaponics. In 2018, hydroponics controlled about 40 percent of the vertical farming market.
Vertical farming businesses develop their own science and mechanical equipment for growing crops. At Living Greens, plants are grown in vertical stacks without the use of soil. The plants are sprayed with nutrient-rich water.
The irrigation is controlled via custom developed software that controls all aspects of the farm. Everything from temperature and humidity, to wind speeds, light levels, and water amounts is controlled, eliminating weather vagaries. Anderson and his investors put up about $5 million into the research and development side of the business.
“Living Greens Farm was a science and engineering operation for many years while we worked to make our proprietary aeroponic grow systems commercially viable,” Klingler said. “There were many challenges along the way. Many different versions of the systems were developed, tried, scrapped, or refined. That went on for years.”
Water from Faribault is distilled and treated to provide the plants what they need to thrive in a “spa-like” environment, Klingler said. “We use inorganic salts to enrich our water. Using inorganic salts allows our growers the ability to choose the individual components the plants need to survive and thrive,” he explained. “Inorganic salts also enable the plants to be able to obtain the nutrients they need in the specific ionic form they prefer. Organic nutrients tend to be in a more basic form and the plant then has to expend energy to convert the organic nutrients into the form they need.”
Living Greens Farm in Minnesota uses a traverse system with a 16-foot energy chain, manufactured by igus, that provides plants with a consistent supply of nutrient-rich water.Photo courtesy of igus
Traverse System with Motion Plastics
Living Greens’ technology includes a traverse system with a 16-foot energy chain manufactured by igus, the Germany-based manufacturer of motion plastics. The company runs its North American operations out of Providence, R.I.
A water line is set into the energy chain, and the system runs 24 hours a day and 7 days a week throughout the year. Each energy chain disperses 130,000 gallons of water each day, about 5,417 gallons per hour.
Living Greens has 74 traverse systems in place at its Minnesota location, and 12 more at a sister farm. Klingler said the company is also working to license its technology to people interested in starting their own farms in Europe, Asia, and Africa.
Charles Jaskolka of igus, who recommended the energy chain, said the chain acts as a guide to keep the water line in place so that it does not wander or get caught in the structure. “The benefit of an automated system is that it allows for better coverage when watering the plants,” Jaskolka said. “It also doesn’t over saturate the plants because they get a dousing of water briefly and the water has a chance to soak in before they get their next drink.”
Klingler said developing the traverse system was one of the challenges in the company’s development. “We were working in a very small space,” he said. “The carriage needs to travel a relatively lengthy distance with a heavy water line. The main feature that we liked about the igus energy chain was that we could incorporate water hose protection. Water is very important to our operation so protecting that source during delivery was essential.”
The H4-32 energy chain from igus is frequently used in applications that require high speeds and/or accelerations, when quiet operation is required, and for long travels. It is also used in applications where high fill weights are needed.
Energy chains from igus are used in a wide range of applications. The dry-running chains require little maintenance and resist dirt and debris. Engineered composite plastic materials from igus are designed with base materials, fibrous reinforcements and solid lubricants that eliminate the need for external lubrication.
A water line set into the energy chain feeds the plants and feeds the plants, delivering about 5,417 gallons of water per hour. Living Greens Farm in Minnesota has 86 traverse systems in operation to help grow its products.igus
Multiple Advantages
Besides requiring less space and water to grow its products, Living Greens provides other advantages for consumers.
Products arrive at grocery store shelves quickly. Its products are sold at stores in the upper Midwest, and in most instances can be in stores on the same day they leave the facility. Some produce in Minnesota stores is shipped from California, requiring up to 2 weeks of travel time. “It can save several hundred thousand miles of shipping – saving over 35,000 gallons of diesel and nearly a million pounds of CO2 emissions,” Anderson said when the company opened its third grow room in 2019.
Reduced land requirements also make Living Greens Farm and similar businesses appealing for urban environments. The U.S. Department of Agriculture expects 66 percent of the population to be living in urban areas by 2050. Delivering food to those urban centers, which is already a shipping challenge, figures to become even more difficult with increased density.
Farmland is also declining across the U.S. While still a nascent industry, all indications point to vertical farming as an important industry in solving a global food challenge that seems likely to escalate in the decades ahead. “With dwindling amounts of land that can be used for farming, as well as the decreasing amount of clean water available for farming it just makes sense,” Klingler said. “Living Greens Farm plans to play a big part in this path forward and is excited to see what the future holds.”
Dan Thompson is the Product Manager of energy chains in North America for igus.