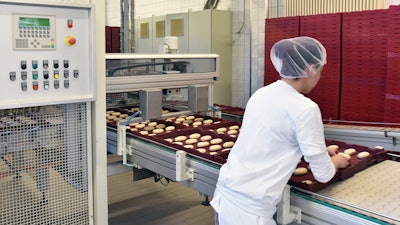
The food manufacturing sector has been in constant flux in recent years. Consumer preferences continue to change, more stringent safety regulations have been introduced and implemented, and heightened demand—as well as disruption—has been present in supply chains.
Because of these factors, food manufacturers are dealing with complex challenges. They must ensure food product safety, remain on top of production timelines, and also maintain sustainable business practices.
With all of that in mind, it is quite clear that traditional approaches to food product development and process management aren’t sufficient any longer. This is where agile product roadmapping software comes into play, as it offers a pioneering approach to streamlining manufacturing operations, boosting overall responsiveness, and realizing sustainable, environmentally friendly growth.
In this article, we’ll examine the most pressing challenges that the food manufacturing sector currently faces and outline the perks and benefits that agile product roadmapping can deliver to companies operating in this industry. The solutions discussed can help food manufacturers adapt to the volatile space they work in and ultimately stay ahead of the curve.
Key Challenges in Food Manufacturing
Now, it’s time to delve into the challenges that food manufacturers regularly experience and the multiple priorities that must be delicately balanced to protect the consumers who place trust in them while also shielding profitability and realizing operational excellence. Understanding these challenges is absolutely necessary to identify best-in-class solutions.
Stringent Safety and Compliance Standards
Quality assurance and regulatory compliance are foundational to the food manufacturing industry. Consumers place trust in these businesses, and guaranteeing public health and safety is paramount.
Ultimately, food manufacturers must adhere to a wide variety of food safety protocols, including Hazard Analysis and Critical Control Points (HACCP), Good Manufacturing Practices (GMP), and food labeling regulations.
These official guidelines require in-depth documentation, regular audits, and intense quality checks to minimize risk and prevent contamination, mislabeling, and/or the presence of allergens.
And the regulations and laws are constantly changing as emerging concerns related to foodborne illness, traceability, and sustainability play a role front and center. Being lax in this area doesn’t only impact quality but can lead to hefty fines and legal consequences.
Supply Chain Disruptions and Ingredient Sourcing
While certainly not the beginning, the COVID-19 pandemic was a significant turning point for food manufacturing companies related to supply chain disruptions, particularly when sourcing raw materials and overseeing ingredient availability.
Global supply chains rely on complex networks of suppliers, transportation and logistics, and international regulations—and these are incredibly vulnerable because of geopolitical tensions, natural disasters, pandemics, and more.
The disruptions lead to many problems, such as delivery delays, pricing increases, and material shortages. Because of this, food manufacturers experience real-time uncertainty surrounding production schedules, timeline adjustments, and potential quality issues.
There must be robust contingency plans in place to diversify supply sources—especially because consumers expect fresh, high-quality food products without question.
Cost Control and Resource Allocation
Inflation, the rising cost of ingredients and transportation, and labor expenses place intense pressure on food manufacturers to effectively spend and allocate resources. As raw material prices fluctuate because of global supply chain problems, economic factors, and climate change, manufacturers must be able to realize profitability alongside product quality.
Furthermore, rising fuel prices and shipping delays strain budgets, especially when a manufacturer sources from diverse international markets.
Additional complexity is experienced by labor costs, the demand for higher wages, and workforce shortages.
Food manufacturers must adopt more efficient production processes while streamlining operations and reducing overhead—all without compromising safety or quality.
Sustainability and Waste Reduction
Consumers want food manufacturers to use eco-friendly business practices—and laws and regulations demand it. Companies are expected to implement sustainable methods, including using biodegradable packaging, reducing energy consumption, and minimizing food waste that could be experienced due to inefficient production processes.
Of course, the challenge lies in aligning “green goals” while protecting the bottom line. Introducing eco-friendly practices usually requires a substantial upfront investment in new technologies, including energy-efficient equipment and new waste reduction systems, which lead to higher operational costs being experienced in real time.
What’s more is that sustainable ingredients or packaging are typically more expensive as well, which further eats into profit margins.
However, despite these challenges, many food manufacturers are also realizing that adopting a green mindset can also lead to long-term savings, improved use of resources, and a positive brand perception on behalf of customers.
Innovation and Product Development
The increasing demand for new and innovative products is a defining factor in the food manufacturing industry, especially as consumers’ tastes and preferences continue to evolve.
Consumers have a growing appetite for plant-based foods, allergen-free options, and clean-label products that address health-conscious and environmentally aware lifestyles.
This, ultimately, requires manufacturers to innovate rapidly and develop new recipes and formulations that meet diverse consumer desires while guaranteeing taste, quality, and nutritional value. Of course, though, this brings its own set of challenges related to production speed and flexibility. It’s non-negotiable for a food manufacturer to develop new approaches to how they do business in order to remain competitive.
How Agile Product Roadmapping Software Can Address These Challenges
In this next section, we’ll explore how agile product roadmapping software can help food manufacturing companies overcome the issues that have been discussed, from ensuring compliance and managing supply chain disruptions to making their businesses “greener” and embracing innovation.
Centralized Compliance and Safety Management
Agile product platforms can improve centralized compliance and safety management. This technology accomplishes this by offering a streamlined way of tracking and managing compliance tasks.
Food manufacturers can set up automated workflows for safety checks, which confirms that tasks such as hazard analysis, quality control, and sanitation protocols are performed consistently and on-time.
Teams are able to easily access repositories of data, which improves transparency and minimizes the chance something is overlooked.
Furthermore, when regulatory changes occur or new laws are introduced, agile technology can be updated to incorporate new standards. This ensures that the production process is always in alignment with the latest developments—all of which reduce downtime and the chance of legal or financial violations.
Improved Supply Chain Coordination and Risk Management
Agile software enables food manufacturers to realize real-time visibility to the supply chain and adapt accordingly. With flexible plans for ingredient sourcing, manufacturers will be able to manage fluctuations in availability, pricing, and supplier performance.
Moreover, agile tools can let a company track inventory levels, thereby confirming that product schedules are based on up-to-date data, which assists in preventing stockouts or overstocking.
Supply chain disruptions can also be addressed with agile software as it enables the development of contingency plans as new information becomes available.
By taking a proactive rather than reactive approach, there is greater collaboration across teams and suppliers, helping production stay on track, ensuring costs are controlled, and mitigating risk.
Efficient Budgeting and Cost Management
With agile software, teams can plan short, flexible sprints, which benefits budgeting and cost management processes. Production is, in turn, broken down into manageable phases, each with its own set of defined objectives and budgets.
When work is performed in shorter cycles, food manufacturers are able to identify areas for improvement or realize that overspending might occur, implementing a fix prior to escalation.
By adapting to unexpected changes, such as modifying ingredient prices or supply chain delays, teams can fill a gap that traditional long-term budgeting doesn’t account for.
Going a step further, agile tools also allow for better collaboration across an enterprise, bringing together production, finance, and R&D teams, as well as other departments, which delivers alignment on cost targets.
Tracking and Advancing Sustainability Initiatives
When agile software platforms are used by food manufacturers, sustainability initiatives can be tracked and advanced. It offers flexibility in managing and monitoring varied eco-friendly efforts in real-time, which can minimize waste reduction related to raw material usage through finished product packaging.
The business benefits from this because opportunities for recycling, food waste reduction, production optimization, and energy use minimization can be uncovered.
By organizing sustainability initiatives within agile software, manufacturers can guarantee that green business objectives are harmonized with financial goals and that efforts to reduce the business’s impact on the environment do not result in a ballooning of overhead expenses.
Of course, this also leads to greater customer satisfaction and brand advocacy because food manufacturers consider the business’s impact on the planet.
Rapid Product Development and Consumer-Centric Innovation
Agile roadmapping is also recognized as an incredible tool when it is used to break down product development into shorter, iterative phases. Teams can better prioritize new product ideas that are based on real-time consumer feedback and market trends.
Whether there’s a growing demand for plant-based products or recipes and formulations that are free of allergens or feature clean-label ingredients, agile roadmaps promote a more collaborative approach to innovation because they bring together multidisciplinary teams. R&D, marketing, and consumer insight groups can better refine concepts, test prototypes, and generate actionable insight.
Therefore, agile software helps food manufacturers bring products to market faster and with greater precision, establishing the business as a leader in consumer-driven invention.
Embracing Agile Roadmapping Software for a Future-Ready Food Manufacturing Industry
There are many significant advantages associated with agile product roadmapping software when it is adopted by food manufacturing companies looking to future-proof their businesses.
From ensuring compliance with shifting safety standards and dealing with supply chain issues to managing budgets and creating cutting-edge products, agile tools are effective at realizing operational excellence and achieving flexibility in a constantly changing market.
Embracing agile software is a necessity in the food manufacturing industry. Take this opportunity to assess and understand the needs of your business—and then look for a tool that is intuitive, customizable, and scalable. Now is the time to put technology in place that allows your business to perform more competitively.