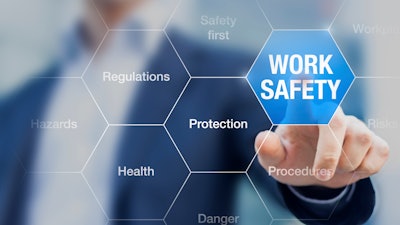
In an era dominated by technological advancements, traditional no-device policies within workplaces are increasingly being recognized as outdated barriers to progress. As industries evolve and safety protocols become more intricate, the need for a digitally connected workforce has never been more apparent. Embracing connectivity can not only enhance workplace safety, but also drive efficiency in modern work environments.
Traditional no-device policies, conceived in an era when mobile technology was in its infancy, were primarily aimed at minimizing distractions and fostering a focused work environment. However, as we stand at the crossroads of the fourth industrial revolution, it is evident that these policies may inadvertently hinder rather than promote safety within the workplace. The advent of smartphones, wearables, and other connected devices has presented an unprecedented opportunity to leverage technology for the betterment of safety protocols.
Many people are already adapting to wearable technology in their daily lives by wearing smartwatches that can monitor heart rate, blood oxygen levels, sleep, stress and activity. According to Statista, there were an estimated 200 million smartwatch shipments worldwide in 2022. That number is set to almost double by 2026. So why isn’t that same trend happening on the work floor?
Traditional no-device policies fail to adapt to the evolving nature of safety practices. In many industries, real-time information is crucial for preventing accidents and responding swiftly to emergencies. Prohibiting the use of devices creates a communication gap that can lead to delayed responses and increase the risk of accidents.
When the workers on the floor are not digitally connected, and there’s a malfunction in machinery, they have no way to immediately alert the maintenance teams or supervisors. This delay in communication can result in prolonged downtime for machinery, safety risks, and delays in production. When workers are digitally connected, the maintenance team and supervisors can be immediately alerted, allowing them to take the appropriate actions needed to address the issue promptly.
Additionally, some technology can even allow maintenance teams and supervisors to remotely troubleshoot the problem. Rapid responses like this can ensure smoother operations. By allowing employees to utilize connected devices, workplaces can ensure that critical information reaches the right individuals promptly, enabling proactive decision-making and minimizing potential safety hazards.
Embracing the New Age
The rise of Internet of Things (IoT) devices has opened up new avenues for monitoring and maintaining workplace safety. Smart sensors embedded in machinery, personal protective equipment and environmental monitoring systems can continuously collect data and provide insights in real-time. Digitally connected safety managers can access this data through their devices, allowing for proactive identification of potential safety issues and the implementation of preventive measures. This shift from reactive to proactive safety management is paramount in reducing accidents and creating a secure work environment.
Efficiency gains associated with a digitally connected workforce cannot be overlooked. Connected devices facilitate seamless communication and collaboration, breaking down silos and fostering a culture of shared responsibility for safety. For instance, instant messaging, video conferencing, and collaborative platforms enable employees to communicate efficiently and share vital information irrespective of their physical location. This not only accelerates decision-making processes, but also ensures that everyone is on the same page regarding safety protocols and procedures.
The integration of digital tools also streamlines incident reporting and documentation. Employees can use their devices to report safety concerns or incidents promptly, ensuring that the necessary actions are taken swiftly. This real-time reporting not only aids in resolving issues promptly but also contributes to the creation of a data-driven safety culture. Analyzing incident data allows organizations to identify trends, address recurring issues, and continuously improve safety protocols.
The era of traditional no-device policies is fading as the workplace landscape evolves and technology becomes an integral part of our daily lives. Embracing a digitally connected workforce is not merely about accommodating modern gadgets; it is a strategic move toward enhancing workplace safety and efficiency.
The seamless flow of real-time information, the integration of IoT devices, immersive training experiences, and efficient communication are just a few of the benefits that a connected workforce brings to the table. As industries navigate the challenges of the future, it is imperative to recognize the potential of technology in revolutionizing safety protocols and creating work environments that are not only secure, but also highly efficient.