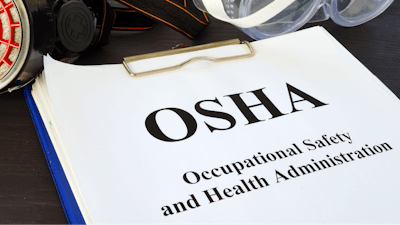
Workplace Safety and OSHA Compliance are critical organizational factors that can easily slip the mind of manufacturers in busy workplaces. However, manufacturers should view these compliance and safety measures as closely related to quality assurance measures. In fact, the same systems that are currently in place to ensure product quality and compliance can be applied to workplace safety and OSHA compliance to ensure high standards are met across the board.
Applying the same mechanisms to workplace safety and OSHA compliance ensures a high standard of clear accountability measures across the company, eliminating duplicative systems vying for limited resources and time. If workplace safety and OSHA compliance management is not already an integral part of the productivity picture for manufacturers, then manufacturers can begin by piggy backing onto these existing protocols to manage efficiency and quality.
The Glue of Operations
It may not be helpful for manufacturers to approach workplace safety and OSHA compliance as an independent goal, because doing so risks workplace safety strategies and OSHA compliance becoming isolated, relegated to the bottom of the priority ladder, or the responsibility of only a few individuals. These individuals often have responsibility but not authority to oversee the safety and compliance standards of the entire plant.
Often if workplace safety and OSHA compliance systems falter, it is due to neglect or lack of prioritization and resources allocated from upper management. This includes the lack of authority given to those managing workplace safety strategies and OSHA compliance, leaving those workers in an impossible position, unable to enact broader measures across the company.
Even the strongest commitment from management to uphold workplace safety standards and remain compliant with OSHA to ensure safety across the business, can be undermined by middle management’s misaligned priorities, resulting in best practices that fail to reach the operational floor. The chain of accountability must be clear and defined for all levels of employees as they are when discussing production quality. Thus, all employees should truly internalize their role in preserving the safety of the entire enterprise. If this is not well understood, safety becomes an afterthought.
Over time, this results in poor safety performance, a culture of negligence, leading to an increase in near misses, incidents, accidents, frequency and severity of claims, and greater non-compliance, along with a potential heightened risk of regulatory consequences. These penalties can be quite painful for manufacturers in a tight economy, especially when the violation seems like a small detail, such as recordkeeping. However, if there are multiple infractions, the penalty can be multiplied by the number of occurrences leading to a big headache for manufacturers if even the smallest detail is overlooked.
If this disconnect continues, heads bang against walls as to the mysterious causes of this abysmal performance. The first sign of dysfunction is the assumption that the fault goes to lazy, inattentive, or accident-prone employees. Upper management may look for someone to blame in these instances. However, unless there is a renewed commitment to workplace safety across the company, newly introduced interventions to improve the workplace safety and OSHA compliance will be seen as additional work burdens, and likely also as “low-value work”.
Safety, like quality, is an organizational issue. Problems that appear are ramifications of systemic errors.
The Price You'll Pay
High safety performance is part of the productivity hygiene formula. Institutional appreciation of the value of prevention and proactivity, and conversely, the cost of the lack thereof, is fundamental and necessary to ensuring workplace safety and compliance with OSHA standards. The quality of the safety management program at a plant is reflected in the efficiency of production, employee morale, with minimal disruptions, down-time, waste, turnover, and tolerable insurance premiums.
Ultimately, workplace safety and OSHA standards have a significant impact on the overall bottom line.
An effective workplace safety and OSHA compliance program begins with a comprehensive baseline assessment to identify different layers and types of issues. This should be both quantitative and qualitative, synthesizing findings into an evolving action plan that acts as a continuous improvement tool and guide for the entire company.
Each action plan should feature written programs and address safety management in a variety of ways, including detailed reporting mechanisms, task protocols and required safety training. Additionally, manufacturers should explore different ways to comply with OSHA standards that meet their individual needs, including personal protective equipment, new engineering or administrative controls or the implementation of new technologies.
Increasing employee engagement in safety measures through the use of safety committees, and self-inspections; checklists; fleet safety programs (if applicable) are also valuable for empowering employees to prioritize safety measures. Additionally, incentive programs can be helpful to reward employees for meeting defined standards of desired conduct and behaviors. These programs should frequently reward the majority and be separate from the number of accidents, which can have negative effects on actual safety.
Ultimately, there are a variety of details that manufacturers need to consider to improve workplace standards and remain compliant with OSHA regulations. Here are some thoughts on how to ensure safety standards receive the same level of attention as product quality:
- Beware of the details - Take a comprehensive approach to OSHA compliance management. Citations are sometimes borne out of ancillary standards. They can be cited multiple times. Ensure compliance with all applicable rules.
- Advanced preparation - Improve inspection preparedness, including being as ready as possible for unannounced (mock) inspections. Penalties may or may not be negotiable, and depending on the nature of the violation, may not be dismissed.
- Written Health & Safety Program & Safety Committee - These are not required by OSHA. However, they serve as evidence of ‘good faith’ and are meaningful assets when negotiating down citations and penalties.
Elsie Tai, is the VP of Occupational Health & Safety Services Group at NFP, a leading property and casualty insurance broker.