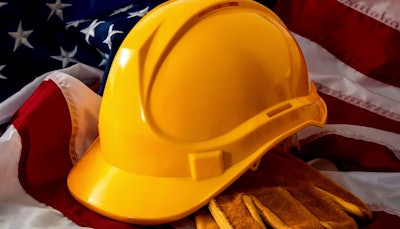
Three years ago, WCCO Belting set the goal of restructuring our safety program to better support our employees - both on the job and at home. As an industrial belting manufacturer, keeping employees safe ensures that we can remain productive and continue to support our customers worldwide in essential industries like agriculture, aggregates, recycling, and others.
Our injury rates several years ago were above the Occupational Safety and Health Administration (OSHA) national average, and we sounded the alarm. To continue to be an employer of choice in our area, we knew we needed to make changes. Since then, we have cut our incident rates in half by focusing on several key areas where safety improvements make a huge impact.
In honor of National Safety Month this June, we’ve compiled a list of the top four ways we embrace safety to keep our incident rates low and to ensure that our employees both come to work and go home to their loved ones safely.
Every “Near Miss” is a Learning Opportunity
Understanding all aspects of safety on the manufacturing floor – and addressing and responding to potential issues – is one of the most important ways we keep our employees safe. At WCCO Belting, we treat every “near miss” like it’s an incident and use it as a learning opportunity. We create protocols to help us avoid future incidents, and we update our employee trainings and our safety manual any time we get new information. Information is willingly shared by our employees as part of shared ownership and responsibility rather than judgement and blame.
Continuous improvement is key to safety success. For example, we continue to work on safety analysis, where we look at each process to find out where hazards exist and how to avoid them. We also conduct bi-weekly safety audits, per OSHA 1910, walking the manufacturing floor while we audit so we can identify red flags before they become a “near miss.” Further, every two weeks we have a team visit the production floor during every shift to monitor safety protocols and look for potential risks.
To take our safety efforts one step further, we also implement protocols that may not be mandated, but that we know will make a difference. For example, we have portable ladders that are OSHA-approved so we can easily reach higher places on the production floor. While it isn’t mandated, we paint the top part of the ladder yellow so it stands out.
Additionally, all forklifts have a blue light that shines out in front and in back so anyone walking near knows a forklift is coming or going. These are two simple yet proactive safety measures we take to eliminate issues. These seemingly small items, and so many others, add up to make a big difference for our employees.
An Employee Suggestion and Reward Program
Through our employee suggestion program, every employee is encouraged to use their voice. Our Kaizen-style program began in 2014, and since then we have received more than 3,300 ideas and have implemented well over half of those ideas. Safety is one aspect of feedback we seek from our employees. To date, we have received more than 610 suggestions involving safety, and we have implemented 64 percent of what employees brought to our attention. Most critical to the successful adoption of this program is acting quickly to implement, or, explaining to the submitter why implementation is not possible or ideal. Now, we are implementing someone’s idea for how to make our workplace better or safer almost every day.
We are also implementing a Safety Standout Award to reward employees for staying safe. Employees will be considered for this award for a variety of reasons, including if they turn in a safety-related employee suggestion idea, if someone identifies a hazard and tells us about it so we can review it and fix it, or if an employee is exhibiting safe behaviors like wearing their PPE, for example. We’ll gather the names of those people for a drawing of gift cards, tickets to community events, or company swag to celebrate those who are being safe on the job.
We also celebrate National Safety Month every June. We host a variety of activities for employees to help them learn about how to be safer in their job. Some examples include a “live hazard” seek and find, a game called “Pin the Pain” to show where injury could occur, abdominal thrust classes, emergency action plan development for home use – including determining emergency escape routes – and many others. To encourage participation, we’ll have a Safety Passport for employees where they earn a stamp for each activity they complete. If an employee completes at least four out of six activities, he or she will be entered into a drawing for multiple large prizes.
Create a Caring, Safety-Focused Culture
We care about our employees and, in turn, our employees on the manufacturing floor care about each other. In fact, we see our employees keeping eyes on each other and looking out for one another to ensure they stay safe, which benefits everyone. When you have a workplace where people authentically care about their team members and keeping everyone safe, you create a positive, caring culture of comradery and support. Additionally, you facilitate the creation of quality products, efficient throughput, and rewarding careers.
As proof of this, one employee and safety team member, Brad, has recruited his entire family to work at WCCO. Brad told me he wouldn’t have encouraged his sons or wife to work here if it wasn’t a safe place to work or build a career. This is a great demonstration of our culture and the impacts we’ve made by focusing more on building and maintaining a safe environment.
In another example, our safety team taught abdominal thrust classes to those who were interested in learning this life-saving skill. Shortly after the class, an employee saved her infant daughter from choking and I, myself, saved my son from choking. Because of our focus on safety and thanks to the training we conducted, we were able to save two children’s lives.
While none of our safety measures are implemented for the sake of recognition, we are proud that for the second year in a row we have received multiple awards from the North Dakota Safety Council. This year, we received the Emerging Safety Champion Award, Workplace Safety Milestone Award, Workplace Safety Merit Award and Lifesaver Award.
Let your Employee Value Proposition be Your Guide
The slogan of our Employee Value Proposition states, “Loving where you work begins with the people you work with.” Our employees – from the leadership team to our manufacturing employees – embrace this and it shows. As Rod, our Vice President of Operations and member of the safety team put it, “I want the team to come to work and go home in the same shape in which they arrived. People don't want to work where they aren’t safe, and keeping employees safe means people are more productive.”
This safety month and beyond, consider how your own facility can implement changes to benefit the well-being of your employees. The return on investment is unparalleled, both for employees and for the business.
Stefani Mikkelson is the Environmental Health and Safety Manager at WCCO Belting, Inc.