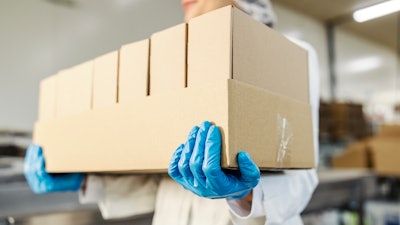
Food manufacturers are at an impasse: with rising inflation impacting the cost of everything from eggs to energy, once-affordable business models — such as investing heavily in single-use packaging — have become increasingly expensive to maintain. At the same time, labor shortages, a lack of automation and supply chain constraints have passed noticeable costs onto consumers, creating market uncertainty and disruption.
While these trends pose challenges for manufacturers and customers alike, innovative tools are being developed to combat them. By making simple but meaningful changes — such as investing in reusable packaging and closed-loop distribution systems — manufacturers can dramatically cut costs while simultaneously bolstering their bottom line. To that end, the following five reusable packaging practices can help food manufacturers enjoy greater sustainability while continuing to turn profits in 2023.
1. Reusable packaging integrates seamlessly into automated systems
Companies are adding in automated systems to help streamline efficiencies and reusable packaging seamlessly complements these systems. Those automation solutions are key during labor shortages: the dimensional consistency afforded by reusable packaging means warehouses can take advantage of more automatic processes while also ensuring fewer production snags and breakdowns. These efficiencies reduce downtime while also helping achieve the throughput speed that retailers — and, by extension, customers — have come to expect.
Not only does reusable packaging cut down on product costs, but it also eliminates labor challenges by considerably shortening the delivery cycle. When used correctly, reusable packages allow ingredients to be moved as food is made, helping manufacturers increase speed and opening the door to new automation solutions.
2. Reusable packaging creates transportation and storage efficiencies
Transportation is another key area where reusable packaging can help cut down on overhead. With growing demand for products and supply chain stress at an all-time high, manufacturers need to maximize their existing infrastructure while freeing up as much warehouse space as possible. To that end, several innovations have made reusable packaging the go-to choice for cutting transportation and storage costs. First, collapsible and nestable packaging solutions allow food manufacturers to devote more warehouse space to production, distribution and repackaging.
Furthermore, for inbound of ingredients and outbound shipments of finished goods, standardized packaging allows manufacturers to transport more product in less space and maximize each truckload. Then, for return shipments, this packaging can nest, collapse or efficiently stack to take up less truckload space and reduce return transportation costs. These kinds of innovations help slash fuel costs while also shortening delivery times.
3. Reusable packaging contributes to profitable sustainability
Once upon a time, “sustainability” was an industry buzzword meant to invoke feelings of environmental responsibility among consumers. Not so anymore. In the modern food manufacturing landscape, sustainability is synonymous with savings: as the price of raw materials continues to increase, continuing to invest in single-use packaging that requires recurring purchasing, creates costly inefficiencies that quickly add up.
At the same time, single-use supply chain packaging contains other sustainability pitfalls — broken boards and protruding nails can harm workers, damage products and contaminate food that might otherwise make it to the grocery store floor. Not only does helping retailers reduce shrink through the implementation of plastic pallets and collapsible boxes improve ROI, but it also contributes to a stronger, more sustainable supply chain.
4. Reusable food packaging can be used to improve hygienics
Almost all food manufacturers are familiar with the wood pallet. While they remain a manufacturing and distribution staple, wood pallets suffer from a number of unhygienic factors that make constant reuse unsafe.
On the other hand, reusable packaging systems, such as plastic pallets, offer far fewer hygienic concerns than wood packaging. Plastic pallets are nonporous and don’t absorb moisture or odors. Plastic pallets are cleanable and can reduce the risk of contamination, and also improve ROI by offering greater dimensional consistency, a longer useful life and lower costs due to an increasingly limited wood supply. These benefits are especially pertinent for food manufacturers that must adhere to stringent FDA regulations — plastic reusable packaging receives far less scrutiny from regulators that may otherwise balk at wood pallet use.
5. Reusable packaging helps create a closed-loop system
The best part about reusable packaging? In addition to other benefits, plastic pallets and reusable boxes can be used to create a closed-loop system that cuts disposal costs and allows for long-term packaging reuse. For instance, delivery trucks that collapse and return boxes, nestable containers and plastic pallets can seamlessly bring them back to warehouse centers to be washed, maintained and reused for future deliveries.
While not every delivery system or food manufacturer can rely on a closed transportation loop, identifying the loops that do exist and taking advantage of them makes sense from both a sustainability and investment standpoint. Doing so improves ROI while also reducing interdependence on single-use packaging manufacturers.
The future of food manufacturing is reusables
While inflation and supply chain issues continue to challenge food manufacturers, efforts to invest in reusable packaging and closed-loop delivery systems can help. Not only are plastic pallets, collapsible boxes, nestable containers and other reusable solutions smart for hygiene, labor, transportation and sustainability reasons, but they also directly contribute to a stronger bottom line for food distributors looking to slash costs and create savings.
Alex Hempel is the senior director, RSC VST at Orbis Corporation.