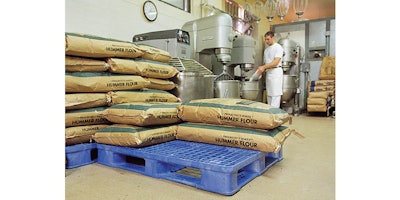
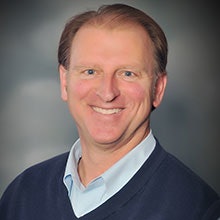
As part of the educational programming offered at PACK EXPO International 2016 in November, the Food Safety Summit again hosted the Food Safety Summit Resource Center. The Food Safety Summit Resource Center hosted 20 30-minute presentations on various topics related to food safety over the four days of PACK EXPO International 2016.
One of those presentations — Best Practices in Implementing Hygienic Plastic Pallets in Food Plants — was delivered by Curt Most, National Pallet Manager, ORBIS Corporation.
According to the presentation synopsis provided by the Food Safety Summit ahead of PACK EXPO International 2016: "Cleanliness and hygiene are critical to today’s food plants. Learn how plastic pallets can be a hygienic solution for handling, storing and moving product throughout the supply chain, from the processing plant to retail distribution. We will take a look at the important characteristics of hygienic pallets and how they can support your sanitation and food safety efforts. From pallet material to design to daily usage in your facility, you will learn how hygienic plastic pallets can support your sanitation and food safety efforts."
Food Manufacturing had the opportunity to correspond with Most after PACK EXPO International 2016 and asked him to provide the top takeaways/highlights from his presentation. The following is his written response:
Hygienic Pallets Defined
Hygienic pallets support the sensitivities involved with food handling. They are easily sanitized, non-porous platforms designed to cleanly move and store food products within a facility to support sanitary conditions. Their one-piece design with no cavities leave minimal areas for contaminants to collect. The open deck allows air flow so the pallets are easy to clean and fast-drying. The contoured surfaces and corners lower risk of product damage due to punctures or snags. Lastly, hygienic pallets do not rust, have nails, staples, lose boards or absorb moisture and odor.
In addition to hygienic pallets, there are other reusable materials that work well in food and beverage supply chains. Top caps create a stable unit load for pallets. They are drainable if left in the rain and keep dust and debris away from products. They also nest with one-piece hygienic pallets to prevent loads from collapsing. They work with a variety of plastic totes, such as ventilated totes, which also stack and nest together. As in the name, they are ventilated for easy cleaning and fast drying.
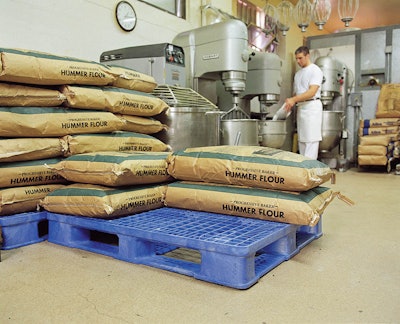
The Food Industry’s Move Toward Plastic
The Food Safety Modernization Act has led to the importance of the type of material handling packing used in supply chains. To abide by the new requirements, more plants are considering plastic material to prevent products from encountering unsanitary conditions. Plastic allows for easy cleaning and allergen management. Plastic also doesn’t retain water, withstands a wide temperature range and allows for color-coding and radio-frequency identification tags. This is why plastic pallets, like hygienic pallets, are preferred over alternates, such as wood and metal. In fact, 38 percent of pallet users are turning to plastic because of the durability and reusability.
Changes in material preferences are uncovering new food plant trends that are being incorporated into modern day plants and retrofitted in older plants. One is the change in automation. Plant engineers have been inspired to design around the pallets versus the other way around. With automation, uptime is key and plastic packaging enables repeatable performance through automated plant equipment.
Second, the performance characteristics of plastic makes it ideal for use with robotics. Plastic packaging is precisely molded and dimensionally consistent, for consistent interface with robotic equipment. Additional new technologies that make up the third trend include:
- Separation equipment
- Pallet washers and rinsers
- Allergen management processes
- Antimicrobial materials
Important Material Considerations
Pallets have many touches with products and equipment on a regular basis, so material selection is critical to the safety of foods and beverages. Before choosing a pallet type, there are multiple material characteristics to consider to meet the FDA-approved material for direct food contact.
These factors include:
- 100 percent virgin content
- Prevents absorption of environmental contaminants like odors, bacteria, pesticides, etc.
- Allows for high temperature washing
- Can be X-rayed and metal detectable
- Custom colored to color code and segregate loads
- Supports labels/hot stamping to identify pallets for lot numbers
- Dust and wood chip free
Also consider the ability of the material to adapt to continuous change. Like many others, the food industry is not short on frequent updates to its best practices and regulations. Not only do plastic pallets have a longer service life, but they can also adjust to new needs such as upgraded automated and material handling equipment, labor practices, production process and material flow to ultimately satisfy customers and consumers.
Five Steps for Pallet Selection
A five-step selection process can help ensure the right pallet material is selected. These tips will help make a decision that is effective for the entire operation, long- and short-term.
- Analyze: Review the products’ life cycle, identify product load characteristics (boxes/cases, powder, liquid), temperature requirements, dimensions and weight, value and load distribution. The level of cleanliness also should be determined.
- Select/Design: Determine the required footprint and pallet style, including stackable and nestable.
- Justify: Compare annual pallet costs, environmental impacts of the alternatives and the characteristics of hygienic pallets.
- Implement: Be sure all of the stakeholders are engaged (operations, material handling, maintenance, etc.) to conduct a small trial. After, be sure all employees are trained on how to use the pallets and each of the features.
- Evolve/Continuous Implement: Do not stop exploring other materials, because like mentioned above, plants will not stop expanding the use of pallets and new technologies, and equipment will evolve to work more efficiently with them. This is why the right material is important in the long run.
Hygienic pallets are a good consideration for food supply chains because of their features that closely correlate to FDA-approved material and requirements under the Food Safety Modernization Act.
Visit orbiscorporation.com to view its hygienic pallet portfolio and the reusable plastic packaging they are compatible with.