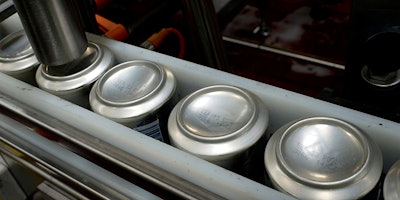
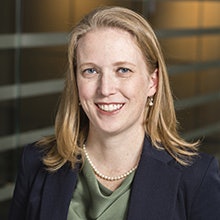
Waste is inevitable on the packaging line. But when packaging line managers find waste, do they treat the symptoms of the problem or do they treat the root cause of the problem? Many opt for treating the symptoms, but from what I have seen, the root cause will always loom over the business, and may create larger problems over time.
So how can you identify and eliminate the root cause of waste in your packaging line?
Most waste is hidden by compensating behaviors. First, I’ll address how to recognize a compensating behavior and then highlight two of the biggest problems and time-wasters I’ve encountered, and how you can fix them.
What Is A Compensating Behavior? How Do You Identify One?
A compensating behavior is something that you do to make up for, and prolong, finding a solution for a much larger problem. An example: You have a product inspection system that reviews your line to help ensure that you don’t let any bad codes get out. Sounds great, right? You’re preventing bad codes from leaving your plant.
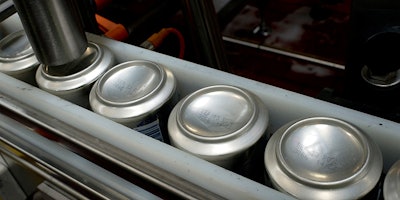
However, your product inspection system is actually a compensating behavior for the things on your line that might be causing you to have the bad codes in the first place. In this case, you’re treating the symptom (bad codes) but not the root cause of why they are there.
Through my work and discussions with line managers, I’ve found three questions to ask that help identify compensating behaviors.
1. How does that step generate value?
Let’s say that you’re a large global beverage company. The value you are delivering is in full, sealed, labeled bottles of soda. But how do you generate that value? In the factory, it may be at the filling machine where the beverage goes into the bottle.
2. How does that step generate value for the customer?
Once you understand how a step in your process generates value, you need to better understand whether that same step also generates value for your customer
A related question might be “if it’s not contributing value, why are you doing it?” and using other “why” questions to figure out why you do each step. In Lean, we call this the “five whys.” Ask why at least five times to start digging deeper into issues to pinpoint the true root cause of a problem.
Often, once you start digging into each “why,” you’ll realize that there are certain actions or processes on the line that have continued to simply mask bigger problems. While the masking works, it also wastes time in the overall process, preventing you from hitting the day’s production targets. Why not just get rid of real problem? Go to the root cause and fix problems that shouldn’t occur in the first place. It may be a change in philosophy for your team to look for these deep-seated problems on the line by asking questions, but I promise that it will be a fruitful change.
3. How do you implement countermeasures to the root cause?
Once you’ve identified the root cause, you can also begin to identify countermeasures that you can implement immediately in order to fix the problem. Unlike compensating behaviors, effective countermeasures should actually eliminate the root cause of the problem and provide long-term solutions.
In the case of the product inspection system and codes mentioned earlier, the real problem might be with the printer that places the codes on the product. It might need servicing, or you might need a new printer entirely. So instead of implementing a product inspection system, the appropriate countermeasure could be replacing the printer — saving both time and money in your overall packaging line process.
Now that you better understand compensating behaviors, I’ll discuss two of the most common types of waste I’ve seen on a packaging line.
1. Pushing Aside Partial Pallets With A Robotic Arm
Many factories push partial pallets off to the side of the line instead of sending them to the rest of the warehouse. They do this just because it’s a partial pallet, something not easily accounted for.
This is actually a compensating behavior, because you’ve invested a lot of money both in the robotic arm and in the physical space for a pallet-sized holding area. Factories that are using this process may be spending money to do this because they don’t know how to disposition a partial pallet. However, if they can figure out why they are filling so many partial pallets in the first place, they can increase both full pallets and overall shipments, while saving money and cutting unnecessary waste.
2. Fear Of Operator Error
Line managers often review everything a line operator does in fear that an operator might have made a mistake. Checking the line’s progress every 15 minutes, or triple-checking work are big compensating behaviors. Line managers need to ask why they are checking work so frequently. In many cases, the root cause stems from variances in how each operator does the same job. However, if operators are provided with specific instructions on the line’s process from the start, there is more consistency and less room for error. That’s why packaging line managers should consider implementing Standard Work.
Standard Work is a guide that operators can use to quickly identify their daily tasks and expectations on the line. It should be straight-forward enough that any new operator can follow and implement daily packaging line tasks correctly and efficiently. By applying Standard Work, you’re reducing the opportunity for errors because every operator is following the same guidelines and process.
In general, once you start asking key questions about common problems on your packaging line and pulling on the thread of compensating behaviors, you will inevitably find the root cause of your packaging line problems. And once you start correctly identifying waste on your packaging line, you be able to implement process improvements and countermeasures that can enable your packaging line to succeed.
Jessica Wettstein is Director of Product Planning at Videojet Technologies.