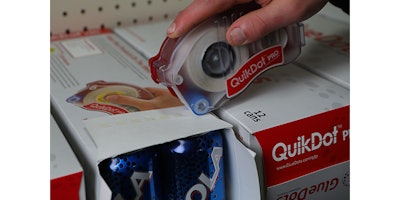
Packaging is a critical component when it comes to marketing food products. A package’s design, shape, size and color play key roles in whether or not it connects with consumers.
An invisible but crucially important aspect of packaging design is the adhesive employed. The wrong adhesive can make a big difference in the overall presentation. Improperly sealed flaps or products slipping out of a windowed box can damage a consumer’s confidence in a brand, not to mention cost time and money to repair.
To avoid these costly scenarios, you need to understand the strengths of different types of adhesives and match them up with the applications they’re designed for. This positions your food packaging to best connect with customers and ultimately lead to increased sales.
Hot Melt Vs. Pressure-Sensitive Adhesives
Hot glue is the go-to adhesive for many food packaging applications, thanks to the speed at which it can be applied and processed, and its relatively low cost. Hot melt is applied to packaging in a fluid state — once it cools, the bond is set.
However, many manufacturers are coming to realize that typical packaging hot melt isn’t ideal for all food packaging applications. This has opened the door for pressure-sensitive adhesives (PSAs) to gain in popularity as a safe, reliable and cost-effective alternative.
PSAs form a clean, instant bond when pressure is applied to join the adhesive to a material. This type of adhesive offers several advantages over hot melt and liquid glues.
During application, the temperatures of typical hot melt can reach between 250°F and 350°F, which can easily cause burns if the adhesive is misapplied or the operator accidentally comes into contact with the equipment. Using hot melt applicators and guns requires workers to be trained in their proper use, as well as wear personal protective equipment such as overalls, protective gloves and safety glasses. Since cold-applied PSAs don’t require heat for application, the threat of burns is eliminated.
Training isn’t a huge extra cost, but it is time that needs to be accounted. In areas where employee turnover is higher than normal, the time and resources to complete employee training on hot melt applicators and guns can begin to quickly add up. Whether using a manual or automated applicator, cold-applied PSAs require virtually no added training.
Cold-applied PSAs also save time in other ways. Because they form an instant bond, they eliminate the cure time or drying time needed by hot melt or liquid glues. They don’t require the heat-up, cool-down or cleanup time of hot-melt equipment.
In addition, cold-applied PSAs give you a consistent amount of adhesive every time. There’s no wasted glue or risk of excess glue making a mess or damaging packaging.
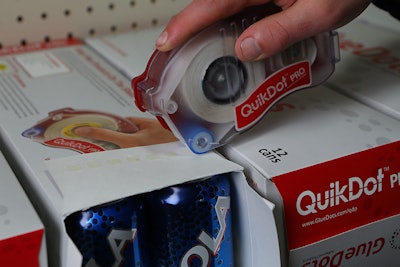
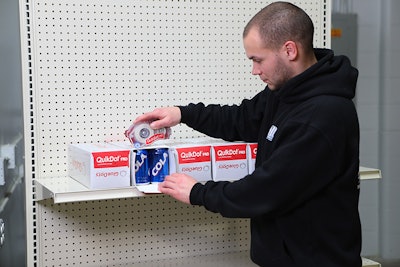
Applications
Because they are quicker, safer and less messy than typical hot melt adhesive, cold-applied PSAs hit the sweet spot for several food and beverage packaging applications:
- Securing products within packaging
- Efficiently grouping small items together in one package
- Attaching labels, coupons and samples cleanly without waste
- Easy repairs to limit breakage, damage and loss
- Keeping brand labels facing forward
- Keeping product orientation during secondary packaging process (i.e. shrink-wrapping)
- Extending shelf life by securing desiccants or oxygen absorbers
For example, instead of setting aside mis-sealed items to be re-run later, packagers can make spot fixes immediately. In store, hand-held PSA applicators allow store employees to cleanly reseal open flaps and place items back on the shelf for sale, rather than wasting time and money sending them back to the manufacturer or distributor for repackaging. Hot melt doesn’t lend itself well to these types of quick repairs, and double-sided tape is aesthetically unpleasing.
PSAs offer more consistent application than hot melt. Uneven application of hot melt may mean too much glue is applied, causing it to leak past the boundaries. Temperature variances of the hot melt can affect its performance as well. If the hot melt is applied too cool, it will cause the adhesive to “string,” or have a tail. When this occurs, the hot melt strays beyond the target area, potentially coming in contact with the product, causing the packaging to look sloppy.
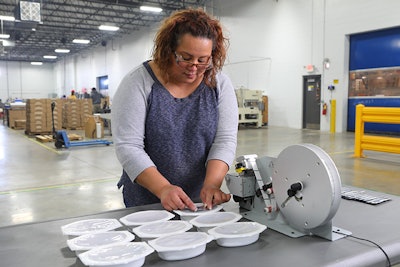
Tack Level And Bond Strength
Since adhesion success is determined by the substrate, PSAs come in different tack levels and bond strengths. An application calling for securing case or carton sealing is much different than a job affixing an adhesive to delicate film. High-tack PSAs can be used to form a permanent seal, while lower-tack formulas can be used to secure samples and coupons so that they can be removed later without causing damage.
It’s also important to identify the characteristics of the substrate. PSAs come with various formulations to match up with different surfaces. For example, is the surface smooth, textured, porous or non-porous, rough or uneven? Knowing this information upfront will help determine the exact adhesive formula needed to form a successful bond. Reputable PSA suppliers can evaluate an application and recommend the best formula and applicator to meet your packaging goals and objectives.
Conclusion
Because pressure-sensitive adhesives provide a strong bond that’s safe and easy to use, they’ve become a reliable, cost-effective option for numerous food packaging applications. They’re ideal for product orientation and grouping applications, as well as on-the-spot repairs. When stacked up against hot melt, cold-applied PSAs are gaining wider acceptance with manufacturers and consumers alike.
Will Cannon is the Industrial National Accounts Manager for Glue Dots International.