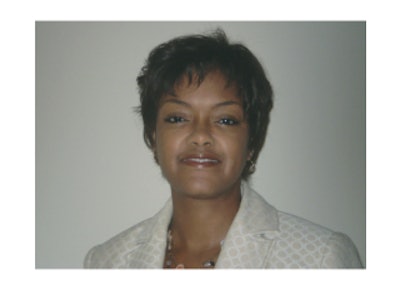
This article originally appeared in the October 2013 issue of Food Manufacturing.
The Food Manufacturing Brainstorm features industry experts sharing their perspectives on issues critical to the overall food industry marketplace. In this issue, we ask: What should beverage processors do to ensure leak-free, robust packaging for their products?
Myra Foster, Executive Director, Global Fluids Sector, Sealed Air’s Cryovac® Food Packaging Brand
Selecting packaging that reduces product leakage is a critical consideration for beverage processors, as leaks can lead to lost product and revenue, potential safety hazards and otherwise increased production costs. Recently, more beverage processors have turned to flexible packaging to benefit from the sustainability advantages it provides compared to rigid alternatives.
Incorporation of flexible packaging introduces some key considerations relative to potential leaks. The most common flexible packaging leaks involve seal failure, poorly attached fitments or closures, or materials not appropriately durable for a particular beverage application. Thus, it is advantageous to partner with a packaging supplier such as Sealed Air’s Cryovac® food packaging brand that operates with a total solutions approach, offering expertise in all three areas.
Flexible beverage packaging should be selected in view of the production, distribution and end usage life cycle of the beverages being packaged. Properly matching equipment and materials with specific attributes can help ensure proper filling and seal quality. Fitments and closures must appropriately and securely seal to the materials and be compatible with filling equipment in the processing facility. A total solutions partner also will work with beverage processors to determine the optimal parameters to protect package integrity — beverages distributed to retailers or foodservice operations can face vastly different transportation, storage and usage conditions which must be addressed upfront in order to select the package with appropriate abuse resistance.
Bob Klimko, Director of Marketing, Retail Supply Chain, ORBIS Corporation
Plastic reusable packaging systems are used by beverage processors and suppliers to move ingredients, cans, bottles and finished goods throughout the supply chain, from manufacturing to the retail floor.
There are examples of robust reusable packaging reducing product damage at every facet of the beverage supply chain. Generally, reusable packaging lends itself to standard and very stable unit loads for shipping, so delivery trucks and full trailers are fully utilized and product does not get damaged during transit. Durable plastic pallets, top frames and divider sheets are used to ship cans and bottles to fillers and are nail free to prevent “leakers,” or punctured cans.
PET bottle suppliers use large collapsible bulk containers to store preforms prior to filling. These containers are designed for stable stacking within a warehouse to prevent bottles from being crushed and damaged. In the retail environment, rugged plastic “shells” are used by bottlers to ship 16-ounce, 20-ounce, 1-liter and 2-liter bottles to the beverage aisle. These shells have smooth internal walls and contoured corners to prevent bottle damage and reduce shrinkage.
Additionally, at retail, bottlers use small-format all-plastic plastic pallets to ship in cases of finished goods. These pallets are free of nails, staples and loose boards that can damage cases, deeming the retailer unable to sell them to consumers. Beverage processors have many opportunities within their supply chain to implement reusable packaging to reduce can, bottle and case damage — from their manufacturing plants all the way to the retailer’s beverage aisle.