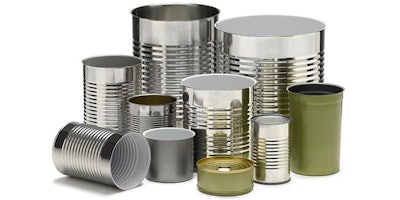
The manufacturers of steel cans are quietly reaching a new milestone in response to consumer preference for new can linings. Years of research, rejection of more than ninety possibilities and extensive safety tests have led to a new reality: today more than 90 percent of food cans have next generation linings — and that percentage continues to increase.
“We listened to consumers and developed can linings that are completely different from their predecessors,” said Robert Budway, President of the Can Manufacturers Institute. “They achieve our top priority of safety while maintaining the quality and freshness of food without using BPA.”
Can linings play a critical role when it comes to food safety. They protect the integrity of the can, preventing corrosion and providing a barrier to bacteria, while maintaining the quality, flavor and freshness of food. Migration of packaging materials from container to food occurs at trace levels whether it’s metal, glass, paper or plastic packaging, which is why it is all regulated. The key to ensuring safety involves extensive data collection and scientific risk assessments.
“The development of safe and effective linings is an intensive, comprehensive undertaking,” Budway said. “The entire process can take five to seven years and every step is important to ensure food safety and protect public health.”
Canned foods have an impressive safety record and those in the industry say they are determined to continue it. More than 3,000 people die and more than 40,000 are hospitalized from foodborne illnesses every year, yet there has not been a single reported incidence of foodborne illness from the failure of metal packaging in more than 40 years despite the consumption of trillions of cans of food. This track record illustrates the commitment of can makers to safety.
Next-generation linings are typically made from acrylic and polyester materials, which are subject to intense scrutiny. Before can linings are taken to market, they undergo extensive testing, analysis and regulatory clearances.
The process involves filling hundreds of cans with different foods, storing them at varying temperatures to mimic realistic conditions and periodically opening a percentage of them to ensure there are no defects of any kind. Every can is also tested for container integrity. Light detectors or air pressure testers are used to detect imperfections. Cans showing any type of weakness are rejected.
The industry’s core principles of safety, integrity and sustainability are reflected in next-generation linings, which exceed the food safety requirements of regulatory agencies and help to meet sustainability goals.
Data shows can makers are using 30 percent less energy and have reduced their carbon footprint by more than 45 percent over the last 20 years, leading to cleaner water, land and air.
Additionally, food cans are the most recycled package in America. Steel is endlessly recyclable, which means that it may be recycled again and again without loss of strength or quality. In fact, 80-90 percent of all steel ever produced is still in use today.
The industry plays an integral role in the overall food system, providing more than 20,000 jobs across the United States with a total payroll of more than $1.5 billion. The total estimated economic impact (direct and induced) of can makers on agriculture, construction, manufacturing and other U.S. business sectors is more than $7.7 billion.
The evolution of can linings demonstrates that can makers are listening to consumers and responding.
“Can makers and can lining companies take very seriously our responsibility to provide safe, quality packaging that consumers trust,” Budway said. “Safety is our number one priority and we’re proud to contribute to a healthy, affordable food supply in a way that reduces food waste and respects the environment.”
Sherrie Rosenblatt is Vice President, Marketing and Communications for the Can Manufacturers Institute.