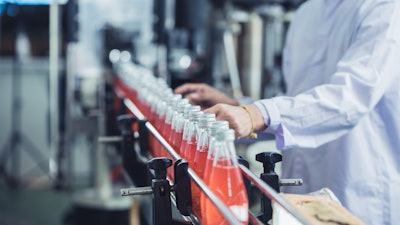
As food manufacturers attempt to scale amidst economic uncertainty, efficiency is more vital than ever. The margin for error has shrunk significantly with rising processing costs, supply chain disruptions, and labor shortages continuing to disrupt the food and beverage (F&B) industry. Cost inflation is aptly reflected in the US Bureau of Labor Statistics’ producer price index, which reached an all-time high in the second half of 2022 and has remained steady since. To complicate matters for manufacturers, U.S. Bureau of Labor Statistics’ reports show that around 750,000 jobs are unfilled in the manufacturing sector, despite unemployment being at historically low levels. The extreme shortage is echoed by Deloitte’s prediction that 2.1 million manufacturing jobs will remain unfilled in the U.S. by 2030.
Manufacturers must find ways to scale with the understanding that labor forces will be serving in a limited capacity. The room for growth is available, as revenue projections in the food market amount to $996.40 billion in 2023. The market is expected to grow annually by 3.4%, but leaders must be prepared to leverage key technology solutions to supplement an expanding skills shortage. Relying on legacy technologies and manual processes will only exasperate challenges.
Scaling without the proper technology and infrastructure in place brings forth a new set of hurdles. Relying on manual processes hinders the agility and transparency of manufacturers, leading to inefficiencies and inconsistencies spanning financial reporting, warehouse management, quality control, and regulatory reporting. These issues stall growth and put businesses at risk of non-compliance with regulatory standards. Manual processes also create a culture of tribal knowledge among employees, and loss of these key employees can be detrimental to the business. Without technology setting clear standards and reflecting efficient workflows, training, and onboarding new employees is incredibly difficult. Given pre-existing labor challenges, this hiccup can’t be afforded.
Fortunately, enterprise resource planning (ERP) solutions are offering manufacturers an opportunity to easily scale and create more efficient and safe practices. Let’s dive into how ERP can aid manufacturers, while protecting against external disruption.
EDI enhances the benefits of comprehensive ERP solutions
ERP technology facilitates scaling by enhancing production efficiency, improving quality and repeatability, as well as lowering labor demands. An integral component to enhancing any ERP solution is beginning an Electronic Data Interchange (EDI) initiative. EDI is a computer-to-computer exchange of documents between trading partners. For many manufacturers, EDI is not a choice – but a requirement for doing business. By embracing this methodology, operational costs can be lowered, efficiency increased, and supply chains become more visible and accurate. The right ERP solution will support your EDI push.
ERP automation technology drives food and beverage manufacturer growth
When upgrading outdated technology and leveraging new solutions, it’s important to keep in mind industry specificity. Whether you are a beverage producer and need more control over your tank scheduling or are an ingredients manufacturer that requires greater insight to trace all your raw materials – F&B specific ERP provides the industry expertise to help run your business with software that meets your specific needs. ERP quickly enhances overall production efficiency through a material requirement planning (MRP) system that can easily take the place of manual scheduling. MRP can automatically calculate demand based on sales orders, schedule production jobs, and identify additional requirements. ERP with a built-in MRP system provides the ability for food manufacturers to plan and schedule production at multiple locations, track different lead times by material, and gain visibility into demand and inventory availability.
As manufacturers scale, one of the most difficult challenges is maintaining the same level of product consistency, and even more importantly, quality. ERP helps to improve F&B product safety and traceability across your entire supply chain. Recent challenges have strained manufacturers, resulting in a rising quantity of recalled products. To support adherence to the Food and Drug Administration’s (FDA) identification and traceability regulations for food manufacturers, ERP solutions utilize lot tracking, asset tracking, and serialization to allow users to identify and trace material at each stage of the product life cycle. Baby formula manufacturer Nature’s One used ERP automation to uphold and manage its stringent regulatory compliance requirements set by the FDA. During recent baby formula shortages, they were able to help address the crises by safely ramping up production. Even in turbulent time, ERP provides the visibility to track and trace each ingredient from the moment it enters the facility as a raw ingredient through its shipment as a finished product.
Combatting the labor shortage amidst scaling
While manufacturers continue to grow, they must do so with a careful eye towards the capabilities of their workforce. As the gulf between labor needs and availability widens, ERP solutions can allow companies to maneuver complex operations regarding supply chains and inventory, helping them to track and automate routine tasks. This greatly alleviates labor requirements. As a result of implementing an ERP solution, co-manufacturer of chocolate and candy bars, Simply Natural was able to reduce their warehouse staff from 10 to 7 people. The company is also able to perform reliable cycle counts just once per week instead of daily, saving the team an average of 8 hours every single week, or 32 hours per month. With small margins for error, these measures of efficiency are big difference makers.
Investing now spurs future success
To stay competitive, manufacturers must leverage technology in times of turbulence. Manual processes impair the ability to scale, and especially the ability to scale efficiently. As companies grow, ERP becomes an integral step in improving production efficiency while maintaining quality standards, all while resisting the external labor challenges. An industry-specific ERP solution helps streamline processes and improve your company’s overall efficiency. This flexibility is required in today’s age of modern F&B manufacturing.
Matt Heerey is the president of manufacturing at ECI Software Solutions.