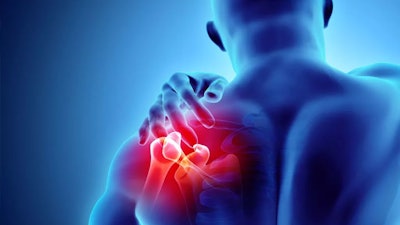
The food and beverage processing industry, like many others, has gone through a significant transformation through the pandemic. It continues to grow as ever before:
- Food and beverage products made up the largest segment of consumer-packaged goods at 44% in 2020.
- Globally, the food and beverage industry is projected to grow to $7,525 billion in 2023 up to nearly $12,000 billion in 2030.
However, major shifts in the industry could challenge manufacturers’ ability to capture this growth. For instance, online food and beverage sales, including delivery and click-to-collect models at grocery stores and restaurants, are surging. Many manufacturers now need an ecommerce channel.
It’s in food and beverage manufacturers’ best interest position themselves to adapt. And a strong workforce is a critical ingredient for adaptability. If your employees don’t feel safe and supported, you’re working off an unstable foundation for growth and change.
Here, we’ll cover current industry trends and stakes, and we’ll discuss why improving ergonomics is a foundational step towards supporting employees and securing your workforce.
The Food and Beverage Industry Shake-Up
Online sales for packaged food and beverage products could reach $109 billion in 2021. This includes delivery and click-and-collect grocery models. In the U.S., ecommerce revenue in food and beverage was $18.7 billion in 2020 and is projected to reach $25.7 billion by 2025.
As a result, using ecommerce for direct-to-consumer models is important for food and beverage processors. Delivery and click-to-collect grocery models are priorities for stores and restaurants. And many consumers now prefer online delivery versus going to restaurants, which affects production planning in terms of packaging and quantities.
Other factors have caused further turbulence for the industry:
- Supply chain disruptions, labor shortages, health and safety concerns, worker strikes, logistics issues and pandemic restrictions are challenging manufacturers’ capacity to reliably fulfill production needs.
- An unstable supply chain has challenged manufacturers, as well as stores and consumers, to find alternatives.
- Shoppers are less loyal to brands after shortages and inconsistencies during the pandemic, and they’re more open to new products.
- Consumers are putting values above price sensitivity, more closely considering ingredients, sourcing, location and processes.
The Food and Beverage Global Market Report 2021 offers several strategies for food and beverage manufacturers to continue to provide value against today’s trends, such as incorporating more natural ingredients, producing more clean label products and implementing automation and robotic technologies. Other shifts might include changing product packaging to accommodate delivery versus restaurant dining. However you shift, investments that improve employee well-being should always be a priority.
Commitment to Your Workforce is Paramount
Amid such turbulence, employee safety and well-being are paramount. Prioritizing investments that improve employees’ daily tasks helps them enjoy their work, reduces the chance of injury while improving productivity and proves your commitment to them. It also helps you retain a reliable workforce during intense labor shortages and employee unrest, avoid worker absences due to injuries, and earn a reputation for valuing your team – which today’s buyers are paying attention to.
Food and Beverage has a High Risk for Injury
The U.S. Bureau of Labor Statistics reports there were 1,643,700 employees in the U.S. food and beverage manufacturing industry by September of 2021. And around a quarter of manufacturing sector accidents happen in food and beverage. Lifting is one of the primary causes of injury in F&B. Whether it’s repetitive or sustained, heavy or light, small or large, lifting can lead to strain and injury. It’s even more challenging when the load is unbalanced or difficult to grip or hold.
Integrating lift assist devices into your processes can improve ergonomics, reducing the likelihood of injury, worker absence or a worker leaving due to safety concerns.
Each task in food and beverage has its own risks and ergonomic hazards. Examples include:
- Lifting, whether repetitive or sustained, heavy or light.
- Moving, such as removing and placing.
- Handling, such as in packaging or inspecting.
- Loading, as with loading on a truck.
- Maintaining an uncomfortable body position, such as stirring in large vats.
Common injuries include:
- Musculoskeletal disorders (MSDs) – Injury/strain to specific parts of the back, wrists, neck, shoulders, etc., such as joints and intervertebral discs, from handling and lifting, often repetitive in nature.
- Work-related upper limb disorders (WRULDs) – Injury to the back and/or shoulders from lighter, repetitive lifting, pushing and handling, often involving physical contortions and bending.
- Strains and sprains – Injuries due to strain in handling. These are the most common, according to the U.S. Bureau of Labor Statistics.
Fatalities also occur in food and beverage manufacturing. The Bureau of Labor Statistics reports there were 41 fatalities in food manufacturing in 2018 and 49 fatalities in 2019.
Many sprains, injuries and accidents can be avoided with lift assist devices and other facility equipment that relieves workers of loads and repetitive tasks.
Work-Related Injuries are Costly – in Many Ways
Injuries can have long-term, permanent effects on individuals and their families. Even short-term sprains with short recovery times can greatly affect a person’s life. You want your employees to have positive experiences and feel safe, not to be burdened by avoidable hazards each day.
Still, there’s a high rate for injury in F&B. The U.S. Bureau of Labor Statistics reported a total of four recordable cases of injury and illness per 100 full-time workers in food manufacturing in 2019. Of those four of 100, 2.8 involved days away from work, job restriction or transfer.
The BLS also reports that data, sprains, strains and tears were the leading incidents for cases that led to days away from work. Soreness and pain came second.
When employees are out, there’s a high cost for manufacturers. They lose production capacity, including the specialized knowledge absent employees take with them. Manufacturers may have to conduct extra training and/or provide overtime to qualified employees. There is also a reputational cost to accidents and injuries in the workplace.
Consider this: By way of the OSHA $afety Pays Program calculator, OSHA calculates that one accident leading to a fracture could cost $54,856 in direct costs and $6,341 in indirect costs. And carpal tunnel, a repetitive injury, could cost nearly $31,000 directly and around $34,000 indirectly.
These costs often outweigh the cost of investing in equipment that enhances ergonomics, such as an industrial lift assist device that renders tools weightless and eliminates issues with operators doing work at awkward angles. Putting those tools in place will enhance employee safety, secure your reputation and save on injury-related costs.
Prioritize Ergonomics for Safety and Savings
The best defense is a good offense. Work to understand the common injuries (or potential injuries based on industry data) and concerns and determine the best preventative remedies.
Implementing lift assist devices can do wonders to improve safety and ergonomics. These devices:
- Take on the weight of the load
- Reduces likelihood of strains and sprains, repetitive injuries and accidents
- Reduced strain enables employees to be more productive
- Enable social distancing in facilities
These benefits lead to reduced costs related to worker injuries.
As part of improving ergonomics at your facility, include training for employees as to proper handling, especially if you’re introducing new equipment to assist them. Also, have a program in place to make sure the protocols and safety measures are being followed, and help employees correct their activities if you see unsafe practices.
The Final Word
Companies that prove they’re investing in the safety and long-term health of their employees by investing in ergonomic lift assist solutions benefit by higher employee loyalty and retention, lower operating costs, and attracting skilled, reliable employees. With the transformation and growth of the food and beverage industry, every advantage in retaining and attracting quality employees will result in big dividends.
Rob Johnson is the Vice President of IPT America – 3arm America, a manufacturer of industrial ergonomic lift assist devices. Contact Rob at [email protected].