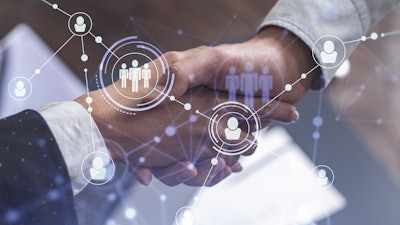
The manufacturing industry is grappling with a significant challenge - a labor shortage that was exacerbated by the COVID-19 pandemic and is now being impacted by the “silver wave” - retirement. To address this issue and attract young talent, Raining Rose, a manufacturing company based in Cedar Rapids, IA, embraced technology and process optimization.
How did Raining Rose overcome the labor shortage? By making itself attractive to a younger generation of workers and adopting advanced technology solutions that GenZ and Millennials expect when starting a job or embarking on a career. The advanced QAD Redzone connected worker solution has not only resulted in attracting younger talent, but also in improved visibility, streamlined operations and increased worker engagement.
When It Rains, It Can Pour
Raining Rose, founded in 1996, grew from a small kitchen hobby into a prominent manufacturing organization. With over 120+ products and two expansive facilities, the company has established itself as a reliable producer of high-quality personal care products.
Before implementing the QAD Redzone connected worker solution, Raining Rose encountered several operational challenges:
- The company relied on manual processes, including spreadsheets and paper-based systems, which hindered real-time visibility and data accessibility.
- Supervisors struggled to maintain continuity across shifts, and workforce retention became an increasing concern.
- Raining Rose recognized the need for a comprehensive technology platform that could address these issues and foster continuous improvement.
After thorough research, Raining Rose selected the QAD Redzone solution, starting with the productivity and compliance modules. This technology offered a holistic approach to manufacturing processes and provided frontline workers with tablet-based endpoint devices, enabling communication across the factory floor. This brought about significant improvements.
One of the most immediate benefits was the reduction and reliance on paper document management, eliminating time-consuming paperwork and enabling easy access to information. Raining Rose gained a comprehensive view of the production process, transforming its operations into a visual factory. As a result, worker engagement and satisfaction increased, with employees having all necessary information at their fingertips.
The new technology also facilitated rapid communication of production changes, ensuring smooth transitions and boosting confidence in workers' abilities. With the ability to identify weak spots promptly, employees offered valuable suggestions for improvement. Raining Rose also experienced a substantial decrease in labor turnover, from 50 percent during the pandemic to just five percent by the end of Q4 2022.
Productivity improvements were notable across various areas, including a 50 percent reduction in changeovers, a 20-point increase in overall equipment effectiveness (OEE), a 57 percent decrease in giveaway, and a 20 percent increase in production units per hour.
Raining Rose's success in overcoming the labor shortage and enhancing operational efficiency serves as a compelling example of the power of advanced technologies, and the impact they can immediately have in manufacturing. Raining Rose's experience demonstrates the importance of embracing technology and continuous improvement to address workforce challenges and achieve sustainable growth.