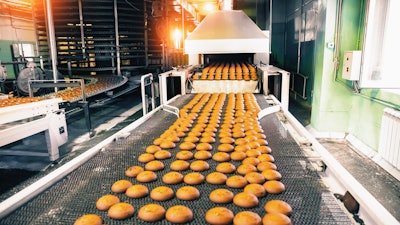
Food and beverage manufacturers have long turned to technology in their efforts to make their operations faster and more efficient.
But with so many other challenges facing those processors, Todd Gilliam, the Americas industry manager for consumer packaged goods at Rockwell Automation, says they’re increasingly thinking beyond production when they evaluate the uses of sensors, controllers and other automation systems.
Gilliam discussed those trends and more in a recent interview with Food Manufacturing.
Answers have been lightly edited for clarity.
FM: What is the food and beverage sector currently looking for when it comes to sensor and control technology?
TG: Traditionally, the goal has been to achieve faster, better, more efficient production. But today, while production optimization remains essential, it’s not the only thing on the mind of food and beverage producers when they build, expand or modernize production lines.
Increasingly, producers are also looking to controllers, sensors and other automation technology to help them solve their biggest challenges of the day. For instance, how will a new technology help them address today’s workforce realities, like changing demographics and scarce talent? Or how will it help them meet pressures from both consumers and investors to create more sustainable operations?
For the workforce issue, food and beverage producers are questioning what work should look like in their operations. Given the tight labor market, they want to determine where they can best use the unique skillset and knowledge of humans, and what activities might be better suited for modern control technology.
Some producers, for example, are using robots like automated guided vehicles — AGVs — to transfer food products, such as from a proofing station to a cooking station. This is made possible by industrial control systems that allow people and robots to work side by side in a safe manner.
Modern control systems that offer enhanced robot integration can also make it easier to integrate, use and maintain robots. For example, engineers can program robots with the same interface they use to program the rest of a line or machine, without needing to learn specialized robot programming languages.
When it comes to creating more sustainable operations, food and beverage producers are discovering that modern control and automation technologies offer inherent sustainability benefits.
A variable frequency drive, or VFD, for example, can deliver significant energy savings when used in place of an across-the-line starter. Similarly, an on-machine drive can use more energy efficient wiring and reduce wear on motor insulation or windings. This can help the motor operate more efficiently and as a result reduce energy usage.
And while sensor technology continues to improve, providing greater visibility into a process and into the health of the sensor itself, such sensors aren’t always needed for sustainability efforts. Instead, in some cases, a basic temperature sensor can suffice. It goes to show how much food and beverage producers can do to address top challenges like sustainability with minimal investments or even the investments they’ve already made.
FM: How are food processors using connected systems and other Industry 4.0 technologies?
TG: The best way to overcome obstacles to growth, like the ongoing skills shortage, or to achieve net zero emissions is with smarter, more connected operations. Food and beverage producers know this. It’s why they’re embracing digital technologies that make their operations – and their workforce – more resilient and agile.
Digital tools, for example, can significantly ease the jobs of production workers. In one case, a dairy producer used OEE software to free its workers from a staggering 2,500 hours of manual data collection. And digital expert-capture tools can be used to retain the critical knowledge of veteran operators or technicians before they retire. Captured information can then be woven into operator instructions, training videos, troubleshooting guides and more.
Greater connectivity and data access is also helping food and beverage companies be more sustainable.
One vegetable oil producer that lacked insights into its energy usage deployed a connected energy management solution that provided visibility into energy usage at the enterprise, site and line levels. The solution also empowered workers with role-based dashboards and predictive and prescriptive analytics. This helped the company identify 10% energy reduction savings.
It’s also important to know that digitalized operations can have valuable indirect benefits. For example, as technology like mobile devices, virtual reality devices and robots permeate a production facility, it can smash the perception that jobs in this industry are dull and reliant on decades-old technology. This can help make a career in food and beverage manufacturing more appealing to younger people who use digital technology in almost every aspect of their daily lives.
FM: What impact is artificial intelligence AI having on the industry, and how is that likely to change in the future?
TG: One of the most popular uses of AI in food and beverage production today is for yield optimization. This can involve the use of model predictive control software, which continuously monitors a process, compares it against previous batches or runs, and drives the process as needed. With each iteration, the software tightens its control of the process based on variables like line speed, temperature and quality measurements until it achieves optimal production within the defined quality specifications.
Model predictive control has proven especially useful in food and beverage applications that have narrow product specifications and critical quality variables. In powdered dairy production, for instance, it’s used to help optimize the drying process that’s both energy intensive and essential to meeting quality specifications. In frozen food production, it helps manage the moisture content that can make or break product quality.
And AI isn’t only proliferating in food and beverage operations in software. It’s also increasingly built into production systems and devices to create smarter, self-aware assets. A good example of this is a VFD with predictive maintenance capabilities. It can alert workers when key components are nearing their end of life, so workers can replace them before they cause unscheduled downtime.