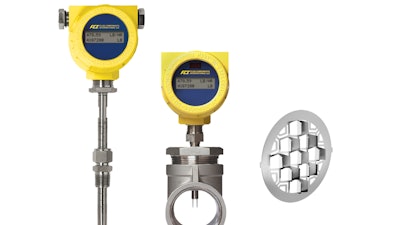
A global manufacturer of recyclable beverage cans has named Fluid Components International (FCI; San Marcos, CA) as a preferred supplier and standardized on the FCI Models ST75AV and ST51A Thermal Mass Flow Meters and Vortab Model VIP Flow Conditioners for the measurement of natural gas in its processes. This is because of their long service life, measurement accuracy and calibration in natural gas under real-world plant floor flow, temperature and pressure conditions.
An engineer at this manufacturer’s plant found that the other flow meters that were installed some years ago to measure natural gas in its heating processes had all failed while the FCI thermal mass flow meters continued to operate without issue. The company then decided to replace its failed meters with FCI thermal mass flow meters based on their longevity, accuracy, and ability to calibrate with actual natural gas.
The process of recycling aluminum cans involves several steps, and it is an efficient way to conserve resources and reduce energy consumption compared to producing aluminum from raw materials. Recyclable aluminum beverage cans are first collected and then sent to recycling centers where they are cleaned, sorted, crushed and next sent to a manufacturing plant.
At the aluminum re-manufacturing plant, the cans are then shredded, melted in large furnaces into a liquid state and then solidified using molds into various sized shapes. The melting point of aluminum is relatively low, around 1200°F (660°C). The molten aluminum is then poured into molds to create ingots or blocks.
The large natural gas fueled furnaces used in these plants are known as a “remelters” in the industry. If the scrap aluminum is coated, it is first processed through a gas-fired rotary furnace to remove the coating and then goes to the remelter. The molten aluminum is then cast into the desired shape before being sent to the can or other type of manufacturing plant for its next life.
For aluminum can manufacturers, being able to measure how much natural gas is used in each process allows them to better understand their current gas consumption to identify opportunities to improve process efficiencies. Most gas lines in these types of plants are 2-inch and smaller, so the inline Model ST75AV Flow Meter is the typical instrument chosen. On larger lines, the Model ST51A with a Vortab® VIP Flow Conditioner is chosen due to the flexibility it provides in placing meters without spending time finding locations with sufficient pipe straight run.
The ST75 Flow Meters are a compact, low cost solution for accurate, repeatable direct mass flow measurement of air and gases. These in-line (spool-piece) style flow meters have no moving parts and are available for use in pipe diameters from 0.25 to 2 inches (6 to 51 mm). They feature wide 100:1 turndown and depending on pipe size, will measure from 0.01 SCFM to 559 (0,01 to 950 NCMH).
The ST75 Series electronics are housed in rugged, IP67 rated enclosure. It comes standard with dual 4-20 mA outputs and a 500 Hz pulse output. The ST75A and ST75AV include HART or Modbus, as well as NAMUR compliant 4-20 mA outputs and SIL compliance rating. The complete instrument carries global Ex agency approvals for Division l/Zone 1 installations.
The Models ST51 and ST51A are a compact, low cost solution for accurate, repeatable flow measurement of biogas, digester gas, landfill gas, methane and natural gas as well as air, compressed air or nitrogen. This insertion-style flow meter has no moving parts and is available in probe lengths for installation into pipe diameters from 2.5 to 24 inches (63 to 610 mm).
The ST51 Series electronics are housed in rugged, IP67 rated enclosure. The instrument comes standard with dual 4-20 mA, NAMUR NE43 complaint outputs and a 500 Hz pulse output. The ST51A adds HART or Modbus, a higher process temperature service range, a SIL compliance rating and extended warranty. The complete instrument carries global Ex agency approvals for Division l/Zone 1 installations.
FCI operates its own world-class, Flow Calibration Laboratory with calibrations performed on more than 19 different flow stands, using equipment traceable to NIST (US National Institute of Standards and Technology), and ISO/IEC 17025 (International Standards for test lab quality systems) and that is certified to meet such stringent standards as ANSI/NCSL Z-540.3. Other flow meter suppliers are often limited to air and water calibrations and then rely on un-validated theoretical equivalencies for other fluids such as natural gas.
FCI solves flow and level measurement applications with advanced thermal dispersion technologies. With almost 60 years’ experience and the largest installed base of thermal flow meters, flow switches and level switches, you can count on FCI to know your application and have the right solutions.